When COVID-19 began, it was clear that people held a wide range of differing ideas about the nature of the disease. Some believed it was “a great plague,” while others said it was “just another flu.” Even among professionals within the built environment, we didn’t quite know what to make of it and the steps we should take to protect those we serve.
Every educational institution had its own unique challenges in dealing with the pandemic; Juilliard was no different. Being a performing arts conservatory, our work predominantly consists of acting, dancing, singing, and playing instruments. Our mission at The Juilliard School is to provide an educational environment for young artists to receive the highest level of training and performing experience so they can realize their true potential as professional musicians, dancers, actors, composers, playwrights, and choreographers in a myriad of career opportunities.
Now came our challenge: What do we do to keep Juilliard going?
We began to review what the experts were telling us. In the beginning, it seemed like opinions and recommendations were changing almost daily, and it was difficult to keep up. We knew that our unique challenges and geography warranted our very best, and we were determined to deliver.
One key topic that emerged as a critical item in protecting against COVID-19 was ventilation. Even more than surface disinfecting, proper ventilation helped to prevent community spread of the disease.
This posed another great challenge. Juilliard’s Irene Diamond Building opened in 1969. Most of the air handling units (AHUs) are over 50 years old. There have been great efforts to maintain these systems throughout the years, but now we were faced with issues related to balance, outside air intake, fan control, and supply volume.
Study Design and Initial Survey
We knew that we had to do something to improve the ventilation of the building. To do that, we needed to know what we were dealing with.
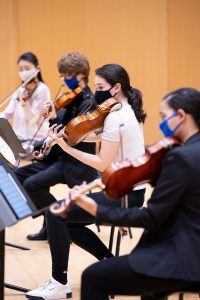
Students rehearsing in Rm 543. Photo credit: Claudio Papapietro.
The Juilliard Office of Facilities Management set out to undertake a study of the building’s ventilation systems with our in-house engineers. This was a first-ever comprehensive assessment of the ventilation systems. Smaller by-zone studies have been done in connection with capital projects and retro-commissioning studies in the past, but this was the first attempt to survey and assess the building as a whole since its construction 50 years earlier.
Following a considerable review of recommendations, we determined that in addition to adequate filtration, optimal ventilation would need to be maintained. Nearly all the AHUs already had MERV-13 or better filtration, and those that didn’t were adaptable to it. For the ventilation, the metric to be used would be air changes per hour (ACH). The minimum target ACH was set at 3 ACH, with 4-6 being optimal. This was calculated by measuring the volume of air being supplied to a space and dividing that by the total volume of air in the room. Understanding that there are other factors involved in calculating the real value of air exchange, we determined that this was an acceptable metric and means of calculation for our circumstances.
For many reasons, this study was conducted internally using only Juilliard staff. Equipment was purchased to measure the ventilation being supplied throughout the building. This equipment has been and will continue to be useful in ongoing testing as adjustments.
The Juilliard engineers were trained on using the equipment, how to measure the volume and velocity of the ventilation, and how to record that in the provided online Excel workbook linked to their mobile devices. The engineers then went out and captured the following data:
- Room ceiling heights, as that was not presently known in the space inventory database.
- Volume of supplied air, obtained by using either a capture hood to measure cubic feet per minute (CFM) or an anemometer to measure feet per second (FPS).
The engineers then entered the data, and the ACH was calculated using formulas built into the provided spreadsheet.
For example, if the volume of air being supplied to the space through the HVAC systems totaled 68 CFM, and the total interior volume of the room was 96 square feet (SF) with a 9-ft. ceiling, the ACH was calculated as follows:
(68 CFM × 60 minutes) / (96 SF × 9 ft.) = 4.72 ACH
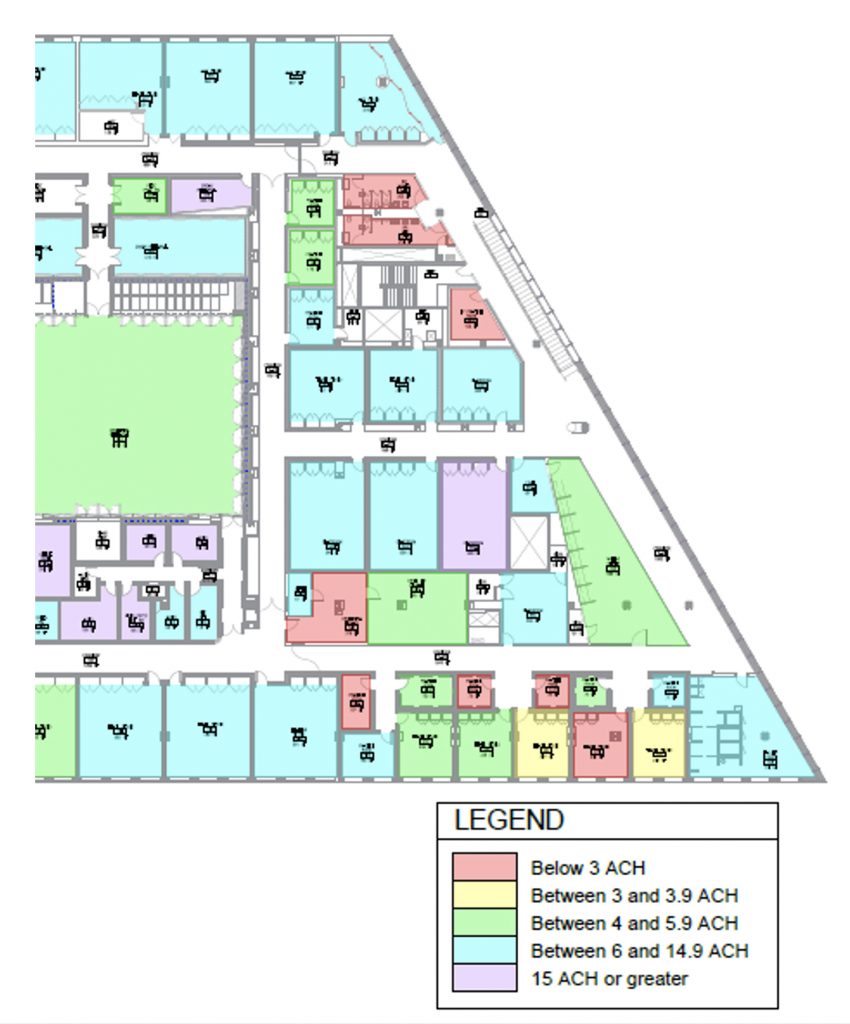
Figure 1: Sample Floorplan
The findings were then classified into the following categories:
- Less than 3 – Too low, Unacceptable
- Between 3 and 3.9 – Acceptable
- Between 4 and 5.9 – Optimal
- Between 6 and 14.9 – High but acceptable
- 15 or greater – Atypically high
Following categorization of the ranges, the findings were plotted on a floorplan of the building (see Figure 1). This assisted with identifying opportunities through juxtaposition and comparison with mechanical drawings of the facility. For example, many rooms that we identified as low volume were adjacent to rooms on the same circuit that had sufficient or even excess volume. < That was an indication we had a stuck damper, clogged coil, or other obstruction that could be easily cleared. If we saw that the entire circuit was low, we knew we needed to look more broadly at that system or AHU for a potential remedy.
Using those tools, recommendations were made regarding individual rooms and fan systems.
Initial Survey Results
An evaluation of the data revealed that some areas had high velocity and required dampening, while others were starved for adequate ventilation and HVAC control. Some areas had stuck dampers or matted coils obstructing flow. The data in this study provided clear illustrations of where the most critical needs were located.
In total, we evaluated 568 spaces totaling 215,728 SF throughout the building. We found that approximately 19% of the square footage surveyed did not meet the acceptable standard for ACH. A summary comparison of ACH readings done before and after improvements can be found further on in Tables 1 and 2.
Improvement Efforts
Following the survey, many recommended actions were identified and pursued including:
- Check and clear stuck dampers and obstructions in ductwork.
- Balance manually operated dampers to provide more capacity downline.
- Evaluate AHUs for opportunities to increase capacity and volume.
Each area found deficient was prioritized into either first, second, or third priority. Work was completed starting with the first priority by August 2020, and all feasible remaining recommendations for all priorities were completed before the start of the spring semester in January 2021. A sample of the report of findings is shown in Figure 2.
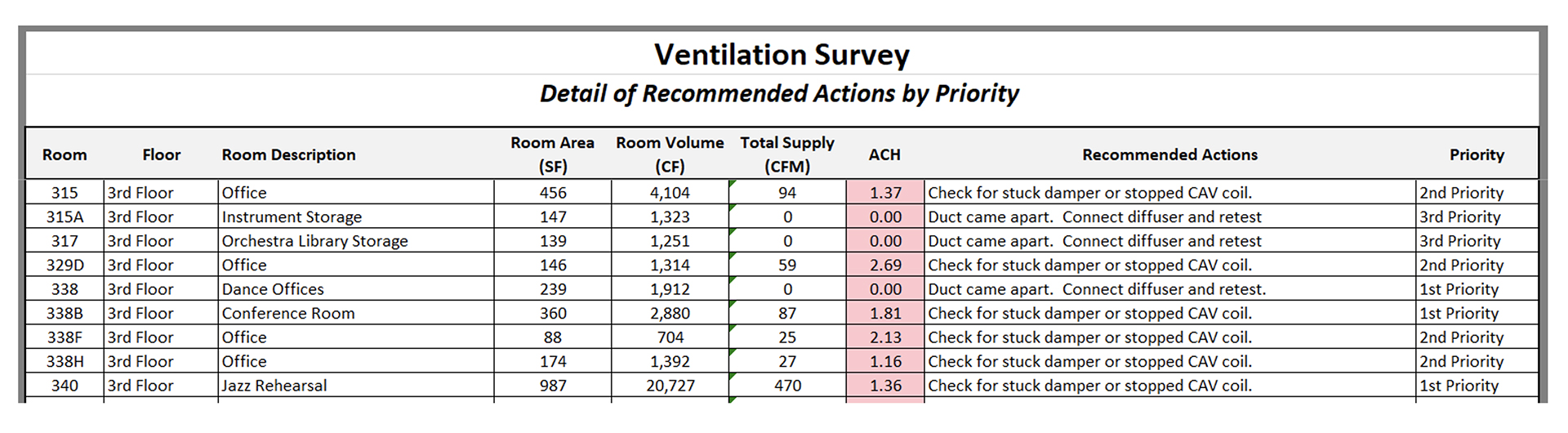
Figure 2: Sample Results Data
In addition, the previous year, the Office of Facilities Management had implemented a new capital needs analysis program that assessed asset life-cycles and condition. From that study, we identified capital improvements that were already funded and shovel-ready before the pandemic hit. Projects to add and upgrade variable speed drives (VSDs) and rehab outside air dampers proved particularly providential for our efforts.
Repairs and Remedies
In all, 182 rooms received improvements. The average ACH of those rooms requiring attention improved from 1.60 to 10.45. Most of the rooms were improved by the completion of basic maintenance activities. The most common remedies are listed below.
- Opened a closed or stuck damper (39%)
- Tested and serviced exhaust systems (34%)
- Cleared obstructions in ductwork (17%)
- Adjusted VSD at the AHU (4%)
- Other remedy (6%)
When asked about these issues, the engineers indicated that many of them were known but they were unable to attend to them because of other demands on their time. At the start of the pandemic, the engineers moved from a 16-hour shop to a 24-hour shop to keep the ventilation systems running longer. The additional time in the building and lower occupancy allowed them greater time to attend to the identified needs and make the remedies required to improve the ventilation.
Final Results
At the outset, it was fully expected that the engineers would be able to have an impact on the ventilation throughout the building. However, the scale of that impact was underestimated. The engineering team did an exceptional service, improving the effectiveness of the existing aging equipment.
Following the improvement work, few rooms remained below the target. Air purifiers were added to supplement the rooms still below target. Ongoing retro-commissioning and other assessments are being pursued to try to address the few remaining needs. Tables 1 and 2 juxtapose the summary findings both before and after the improvements completed by the engineers.
Table 1: Initial Survey
Table 2: After Improvements
Monitoring
HVAC systems are dynamic equipment; just because a survey was completed in August does not mean that data holds true in January. Therefore, a monitoring process was needed to ensure that these systems were proactively tracked. This process consists of three methods.
- Real-time monitoring through the building automation system (BAS). Those few spaces that have received modernized HVAC controls provide the ability to monitor real-time CFM supply to the spaces. Using the integrated features of the BAS, alarms can be set to alert the engineers if one of these areas drops below the required CFM to maintain 4 ACH.
- Real-time monitoring through VSDs. For those spaces that do not have real-time BAS readings of the CFM in the space, real-time monitoring can be accomplished by using the VSD fan speed readout. Through trial and error, the acceptable minimum fan speed required to deliver at least 4 ACH to the worst-case room can be determined. Using the BAS, automated alarms can be used to alert the engineers if the fan speed drops below that threshold.
- Manual Testing. Manual testing is, of course, the most labor-intensive and least predictive form of monitoring. However, due to the age and condition of many of the spaces throughout the school, it is the only option. There are two systems of manual testing that are being employed.
- Weekly Testing of Key Rooms. For rooms that require manual testing and have a greater risk factor (i.e., rooms that have small-ensemble work), weekly testing is administered using the integrated workplace management system (IWMS).
- Sample Testing of Systems. For those rooms that have a lower risk factor, a periodic sampling of rooms within a circuit is being employed. Once per month, a small number of rooms as part of an AHU’s circuit of rooms are tested. If those rooms fall below acceptable levels, the entire circuit for that AHU is retested and evaluated.
Ongoing Efforts
The completion of this project was an exceptional achievement. Not only has an assessment of this magnitude never been done before at Juilliard, but it was also completed with our own internal crew, giving them the experience and saving on the cost. It is the result of great effort by the engineers as well as the tremendous support of the senior administration in reinvesting in the ventilation systems of the facility. This level of effort and reinvestment would be difficult to sustain for the long term without other areas of the operation suffering. As a result, it is not to be assumed that this work is—or will ever be—complete. This work will take continuous commissioning and other ongoing efforts, including staffing adjustments, IWMS adaptation and deployment, and BAS enhancements.
Having a full understanding and comfort level with the ventilation systems was a key component in Juilliard’s return strategy. This work, coupled with other strategic initiatives taken by multiple departments and divisions throughout the school, enabled students to return to limited in-person activity in August 2020, and to incrementally increase activity throughout the school year to the point where they were able to do small-ensemble work and other collaborative in-person work. By the end of the school year, the students were fully ready to deliver nearly 50 public performances.
Many faculty and staff have already commented on the vast difference they feel throughout the building and have expressed their great appreciation. This work, coupled with the ongoing efforts to maintain and continually improve, will help ensure these systems remain as effective assets in the overall building health for the Juilliard community, not only during the pandemic, but long after we have left it behind.
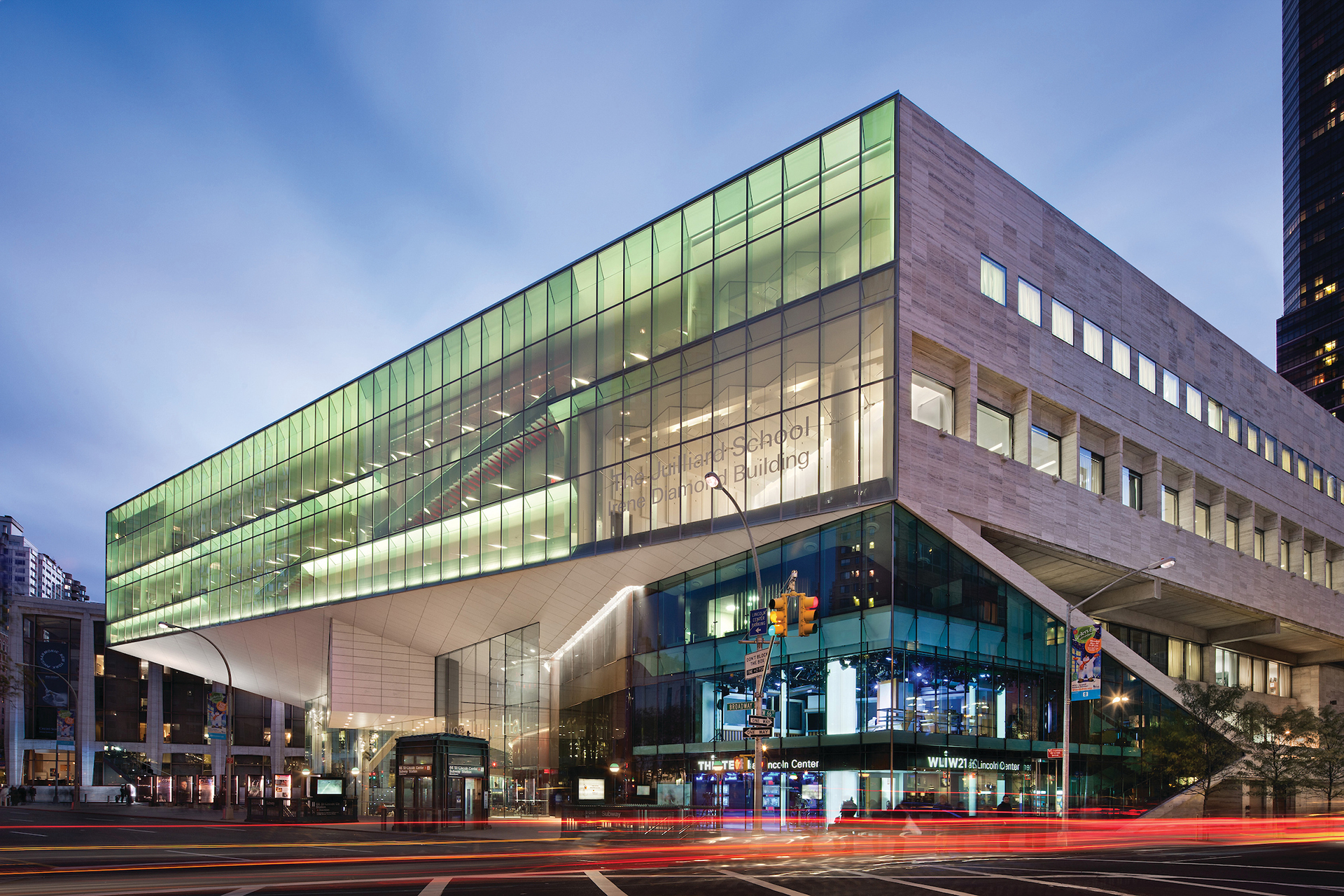
The Juilliard School Irene Diamond Building. Photo credit: Chris Cooper
Bibliography
ANSI/ASHRAE. (2019). Standard 62.1-2019, Ventilation for Acceptable Indoor Air Quality. American National Standards Institute/American Society of Heating, Refrigeration, and Air Conditioning Engineers.
Centers for Disease Control and Prevention. (2021). “Ventilation in Schools and ChildCare Programs.” Retrieved May 15, 2021, from https://www.cdc.gov/coronavirus/2019-ncov/community/schools-childcare/ventilation.html
The Future of Ensembles Committee. (2020). NYSSMA Ad-Hoc Committee Report: The Future of Ensembles – in the COVID-19 Era. New York State Music School Association. https://www.nyssma.org/advocacy/nyssma-covid-19-guidance/the-future-of-ensembles-committee/
Hernandez, D., Toy, S., & McKay, B. (2020). “How Exactly Do You Catch Covid-19? There Is a Growing Consensus.” The Wall Street Journal.
Jones Lang LaSalle. (2020). (Re)open: A Guide for Planning and Preparing Your Campus. https://www.us.jll.com/en/views/reopen-a-guide-for-planning-and-preparing-your-campus
Kohler Ronan. (2020). “COVID-19 Reoccupancy Guidelines” [News Update]. https://kohlerronan.com/covid-19-re-occupancy-guidelines/
Mandavilli, A. (2021). “Airborne Coronavirus: What You Should Do Now.” The New York Times. Retrieved November 10, 2021, from https://www.nytimes.com/2020/07/06/health/coronavirus-airborne-aerosols.html?referringSource=articleShare
Cameron Christensen is associate vice president, facilities, at The Juilliard School in New York, NY. He can be reached at cchristensen@juilliard.edu.