When it comes to the sustainability movement in educational institutions, it sometimes appears to be more talk than action. For example, 83 percent of colleges and universities have campus sustainability committees. However, fewer than 15—not 15 percent, 15—campuses have actually achieved carbon neutrality. That disconnect may be because of seemingly exorbitant up-front costs and logistical challenges required to make sustainable changes to campus buildings and systems.
When modifications do happen, the campus employee most likely to be involved in implementing and maintaining them is the facilities manager. The personnel in those roles should be knowledgeable about the most efficient, durable, and cost-effective ways for their campuses to become more sustainable so they can, in turn, educate campus leaders and potentially effect change. Facilities managers who don’t have the latest information on environmentally friendly campus options or resist making changes risk becoming obsolete when leadership mandates upgrades.
This article informs facilities managers by discussing nine actionable ways campuses can move toward net-zero goals.
1. Replace Steam Systems with Low-Temp Hot Water Systems
Educational institutions can convert from steam heating to an energy-efficient, low-temperature, hot water heating system to be more environmentally friendly. The U.S. Department of Housing and Urban Development (HUD) says steam systems use far more energy than modern alternatives since they require water to be heated to boiling. Many of those steam systems burn non-renewable fossil fuels such as natural gas or fuel oil. That process produces pollutants like carbon monoxide and sulfur dioxide. Newer low-temp hot water systems use heat pumps powered by electricity—a greener energy source.
In Connecticut, Wesleyan University is converting steam pipe systems, some more than a century old, to hot water systems. According to HUD, that conversion can reduce energy costs by up to 39 percent. As the Wesleyan Argus newspaper reports,
“The new pipes will be much more efficient…temperature controlled, equipped with modern insulation, and able to reuse water. The hot water pipes are double insulated with protective high-density polyethylene jackets, technology that didn’t exist when the steam pipes were installed. Hot water pipes also heat to a much lower temperature to reduce energy waste, around 140°F on average. They are also able to adjust temperatures between 115 and 195°F, depending on the weather. The new pipes also eliminate condensation loss, returning all the water they use back to the power plant.”
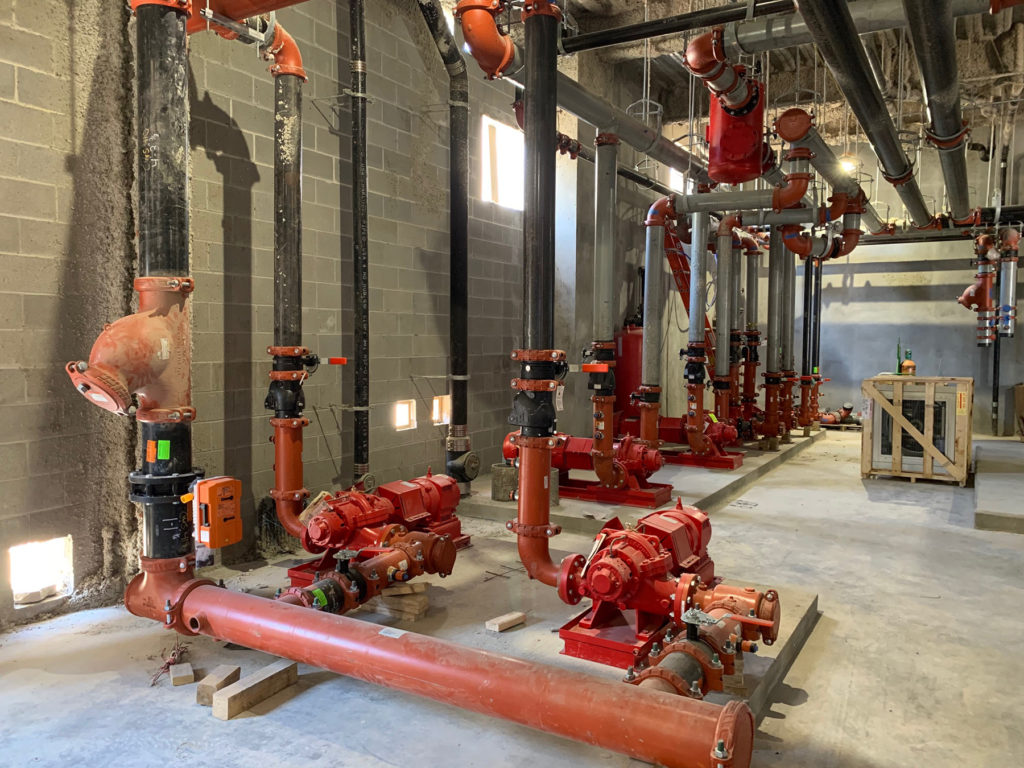
A student center in a northeastern U.S. university utilizes a hot water system in its mechanical room.
2. Move To a District Energy System
Facilities managers must consider the functionality of each building on campus and how those buildings work together. Many older buildings on college campuses operate on their own individual HVAC systems, but converting to a district heating and cooling system connects the campus and has significant benefits.
Changing to a centralized district energy system allows universities to combine facilities’ cooling loads. The rejected waste heat can then be channeled directly into heating loads. A University of Michigan study found that district energy systems help campuses cut greenhouse gas emissions, minimize their carbon footprints, and reduce fuel costs. Additionally, because district energy systems often contain redundancies, facilities managers can be reassured that the systems will have increased reliability during weather emergencies or climate disasters, which, according to the National Oceanic and Atmospheric Administration (NOAA), are increasing in part because of climate change.
3. Use The Environment Available
Thermal is another type of energy system to consider. A thermal energy storage system allows campuses in different parts of the country to save energy by utilizing their own climate. A thermal storage system in North Dakota can store water cooled in winter for air conditioning use in summer. In Arizona, the system can store heat energy gained on blazing hot days that can later be used to power cooling systems in summer or heating systems in winter. The University of Arizona’s thermal energy storage system is one of the largest in the world. The school has seen $38,000 a month in heating and cooling cost savings.
4. Use A Sustainable Design Process
A building’s performance and longevity are optimized when facilities managers are included in the design stage of new buildings, according to a 2021 study. As more campuses are building new, more sustainable facilities, it behooves university leaders to include those managers, and it behooves facilities managers to know how the design process can be more sustainable. Virtual design and construction (VDC) technology enables a more environmentally friendly design-build process than traditional methods. It can expedite construction timelines, reduce material consumption, and decrease the risk of rework. Using building information modeling (BIM) tools to meticulously plan pipe routes can prevent the over-ordering of materials and reduce the number of deliveries during the construction process.
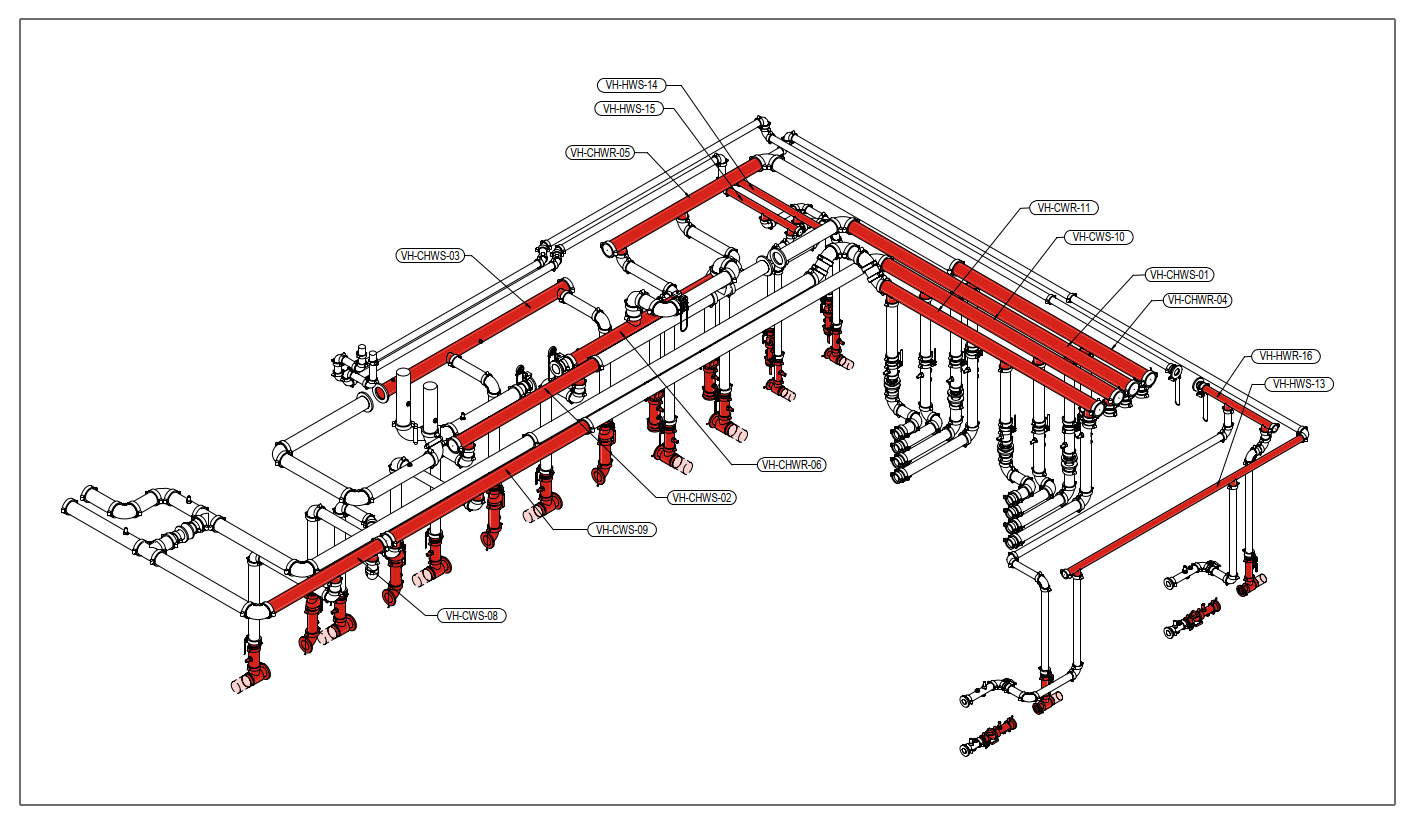
A BIM drawing of an educational building’s mechanical room precisely maps pipe routes to help avoid on-site complications and minimize the risk of rework.
5. Use Sustainable Materials That Are Easy to Install
Talk about unsustainable—some campus buildings have HVAC systems that are more than a hundred years old. These systems create energy inefficiencies and constitute a significant roadblock to sustainability. Facilities managers may be eager for these systems to be swapped out for something newer. Still, they know the changeover can significantly disrupt campus life and want it done as quickly as possible.
Selecting the right materials can help compress construction schedules and minimize disruptions to students and staff. Using grooved pipe-joining technology in mechanical systems can be advantageous because it is simpler to install than other methodologies. The joints can be put in place rapidly with common tools, no matter how large or complicated the project. Installing a grooved system also eliminates the need for welding, which means no open flames or hazardous emissions, including air pollutants and metal fumes. Because of the lower safety threshold, building occupants don’t need to be kept as far away from the work area and can use the building more while a project is in process. Another environmental benefit is that grooved pipe joints are made from recycled material and can be recycled when no longer utilized in a building.
6. Be Mindful of Future Maintenance and Expansion Needs
Mechanical systems that are easier to service, such as those that employ grooved joints, make facilities managers’ jobs easier. They’re more likely to be kept running at peak performance, which saves money on repairs and work hours and allows them to use energy efficiently. Maintenance workers, even those without specialty training and certifications, can easily remove grooved joints if needed. In addition, grooved joints offer greater flexibility and constructability, allowing for easy reconfiguration for future expansion.
7. Switch to Low-Flow Water Fixtures
Low-flow water fixtures are becoming more common in all types of buildings. According to the Environmental Protection Agency (EPA), a standard faucet uses an average of 2.2 gallons per minute (GPM), whereas a low-flow faucet typically does not exceed 1.5 GPM. It may not seem as if such a small change could make a big difference in a university’s water usage, but lessening the water flow from potentially thousands of sinks, toilets, and showers can have a significant impact. This is especially true on campuses where many buildings are decades old. The U.S. General Services Administration reports that many structures built before 1992 may be using more water than the current code allows.
Cost may be a concern, but the fixtures pay for themselves. After installing low-flow fixtures, the University of Illinois reduced its water consumption—and cost—by 40 percent. Savings also come from requiring less energy to heat the smaller amount of water coming through the tap or shower head.
8. Install Rainwater Cisterns
Rainwater cisterns are another way to conserve water. The cisterns are large tanks that collect water running off rooftops. They can hold thousands of gallons. The State University of New York (SUNY) at New Paltz uses water from cisterns to flush toilets and urinals. Western Kentucky University irrigates campus gardens and trees with water from cisterns. This lowers campus water usage and utility costs. In addition, rainwater cisterns reduce pollution in lakes, rivers, and streams by collecting water that would otherwise pick up oil, pesticides, and bacteria as it flows into storm drains and eventually into bodies of water.
9. Upgrade Lighting
Lighting accounts for about 31 percent of a college’s energy costs. According to the U.S. government’s Energy Star program, LED lightbulbs are as bright as traditional bulbs but use 90 percent less energy. The age of many campus buildings makes it likely that they employ older, incandescent bulbs. Switching to LED bulbs around campus can save a massive amount of energy.
Another form of illumination to consider is daylighting. New buildings can be designed or remodeled for optimal use of natural light, requiring less electricity to make environments conducive to learning.
Facilities Managers Can Be a Guide
Facilities managers have many concerns to consider as they maintain and improve their buildings—budgetary constraints, regulatory compliance, emergency preparedness, security, and staffing, to name a few. Making campuses more sustainable may seem like something they can’t add to their list. However, building managers know those steps are necessary for all university stakeholders and the planet’s greater good. Having input from a knowledgeable facilities manager can help leaders evaluate their options and choose the best way for their campuses to move toward sustainability goals.
Brad Smalling is a regional business development manager at Victaulic in Easton, Pennsylvania. You can contact him on LinkedIn. This is his first article for Facilities Manager.