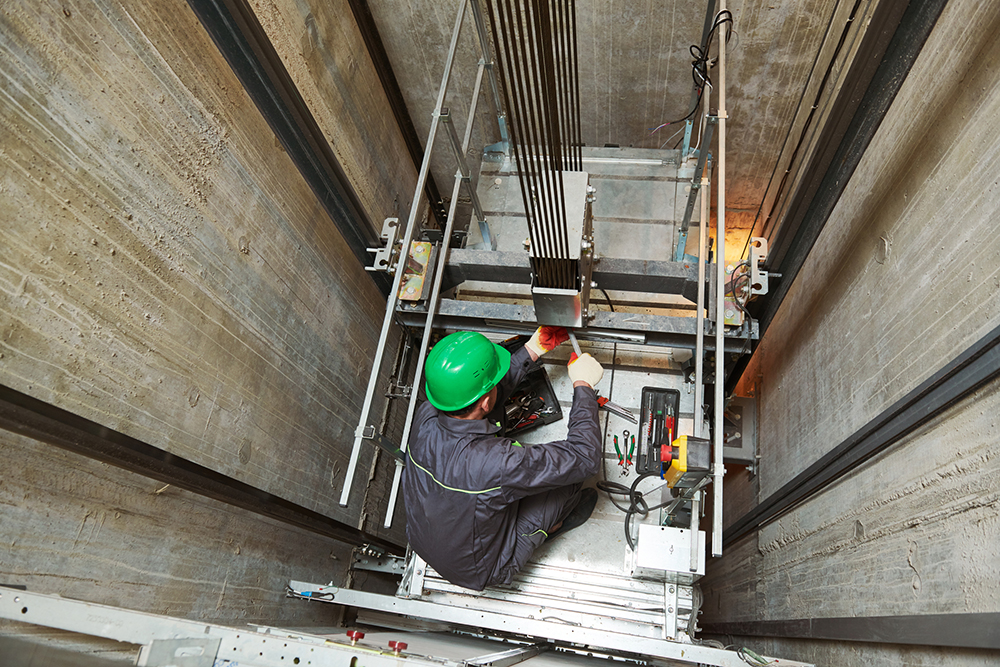
Elevators are a crucial part of any building’s infrastructure, and their continual functioning goes a long way toward making building visitors feel secure. When it comes to managing educational facilities, a nonworking elevator can be a hassle for students and staff alike, but it can also raise larger questions about the institution’s dedication to accessibility and user safety—and may even lead to doubts about the financial stability of the school. Ensuring a learning institution’s elevators are well maintained is mission critical.
Having a good understanding of how long an elevator is likely to last is important, because it will help facilities managers and educational plant administrators strategically plan preventative maintenance programs, modernization timeframes, and, eventually, replacement. Knowing the lifecycle criteria of your institution’s elevators will keep the system running safely and efficiently throughout its lifespan and minimize problems.
It is possible to estimate how long a given elevator and its components can be expected to last. Knowing this ahead of time will, of course, indicate when an elevator or its parts need to be replaced, but that in turn will allow for scheduling, planning, and budgeting of those replacements. For educational institutions, lifecycle planning can be an important component of remaining on pace for needed compliance upgrades and coordinating with infrastructure repairs or additions; it also provides a blueprint to work from in case adjustments need to be made due to budget cuts—or better yet—influxes.
The Typical Lifespan of an Elevator
A variety of factors can contribute to the lifecycle of an elevator, including when it was built, daily usage, environment, and the established schedule of maintenance routines— or lack thereof.
Cab interiors and call stations often need upgrades and replacement ahead of other components, with typical stress and damage over time becoming evident between 10 and 15 years after original installation. But machinery and wiring systems can last well beyond that, with an average lifespan of 30 years or more, before needing to be replaced.
Other parts may have their own timelines for modernization and replacement, including controllers, hydraulic power units, or hoist machines, just to name a few of the critical components needed for a functioning elevator. Most overall elevator systems are built to last at peak operation performance for between 20 and 30 years.
To address the anticipated degradation of parts and systems over time, it’s recommended that educational facilities managers build parts review and preventative servicing into their maintenance schedules and budgets.
Find the Best Service and Maintenance Partner
Whether you want to evaluate your current elevator company or search for a new one, the following checklist can help you determine the right fit:
- Check the company’s references. It is particularly important to see that the company has experience in successfully working with other educational facilities and understands the specific challenges faced in these environments.
- Assess response times. Find out if they are available 24/7 and what their typical response times to emergencies are.
- Assess their expertise. Have they worked on your type of elevator? Do they understand the systems you use? What do they specialize in?
- Understand their ability to switch. Make sure that they are experienced in switching from a previous service company to theirs.
- Evaluate their communications. It’s important to have a service partner that is transparent in all aspects of every project—including billing and compliance.
- Explore their safety policy. A good service partner will put safety first and do everything in their power to keep your occupants safe—as well as their own staff.
Managing the End of an Elevator System’s Life
Repeated breakdowns can cause serious headaches to any facility, but perhaps even more so for educational facilities, where visitors are often getting to classes and meetings en masse on a frequent schedule. Tardiness can affect students’ grades and strain learning relationships with teachers and professors.
Eventually, the typical elevator system will reach a point where it no longer makes good financial sense to continue repairing it. The elevators may keep breaking down, with every repair call adding to the overall cost. Alternatively, the equipment may simply appear tired and worn down due to its age. Most elevator service companies will be able to help calculate the cost of a full or partial modernization as compared to escalating repair bills, and they can also advise on the right time to upgrade.
Another reason for modernizing or adding elevators could be growth. As a campus or educational institution attracts more students and teachers, the number—and size—of elevators need to be reviewed. Access and egress routes must also be considered to ensure all occupants will find it easy to navigate to and from the elevators.
When installing, adding, or modernizing an elevator system, there are specific building regulations for educational institutions that everyone involved in the project needs to be aware of. There may be local legal variations, but generally the minimum platform size needs to measure 1,000 by 1,400 mm, and an elevator cab carrying eight people should measure at least 1,100 by 1,400 mm. The elevator capacity needs to be determined by the expected traffic volume.
Summary
Educational institutions are legally required to make their facilities fully accessible to people of all physical abilities, but they also have a responsibility to help students and staff members get to their destinations as easily and comfortably as possible. This means keeping elevators in good repair, minimizing downtime, and recognizing when an elevator is reaching the end of its lifespan. During times of growth, it’s important to consider how the added footfall impacts the use of elevators—and to adapt as needed to keep traffic flowing well throughout the property.
There is no great mystery to the lifecycle of elevators, but all educational facilities will benefit greatly from having a dependable service partner who can keep them running efficiently and offer guidance on the cost benefits of modernizing when the time is right to do so.
Eric Lazear is vice president of business development at American Elevator Group in New York, NY. He can be reached at [email protected]. This is his first article for Facilities Manager.
Facility Asset Management
Covers the issues and challenges surrounding the management of a facilities department, including solutions for benchmarking performance measures, database and reporting systems, and professional and educational trends in facilities management. To contribute, contact Lindsay Wagner, field editor of this column.
See all Facility Asset Management.