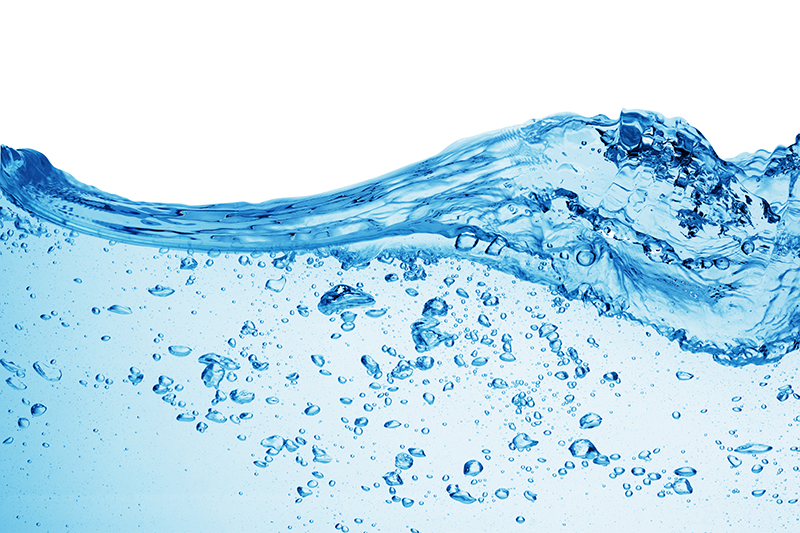
With over 10,000 graduate and undergraduate students and an expanding campus, a private university in Tennessee had a unique opportunity to make a tremendous environmental impact.
In 2014, the institution outlined a broad set of behavioral and operational standards across the campus, designed to reduce energy costs and consumption. The policy included many common-sense provisions, such as shutting off lights in empty rooms and requiring power-saving settings. Additionally, several larger scale initiatives were introduced, such as identifying and implementing energy efficiency opportunities in the campus’s large research labs.
Laboratories, on average, use far more energy and water per square foot than office buildings and other facilities because their activities are energy-intensive and their health and safety requirements are more stringent. Labs can account for up to two-thirds of a large campus’s energy consumption, using up to five times more energy than other campus buildings due to the multitude of ventilation and fume hoods, electrically operated fans, specialized lab equipment, and large quantities of process-chilled water.
As such a large energy consumer, the university’s facilities and operations teams are constantly searching for ways to improve efficiency and cut energy usage, and recently focused their efforts on the expansion of a medical research building. The expansion project included 260,000 sq. ft. of new research and the renovation of a previously existing 85,000-sq.-ft. laboratory.
The campus energy team, overseers of sitewide maintenance and energy, was brought into the fold to help vet efficiency solutions related to the expansion project’s HVAC elements. The team commissioned several vendor energy audits of the building’s cooling system that allowed them to identify and analyze costly inefficiencies.
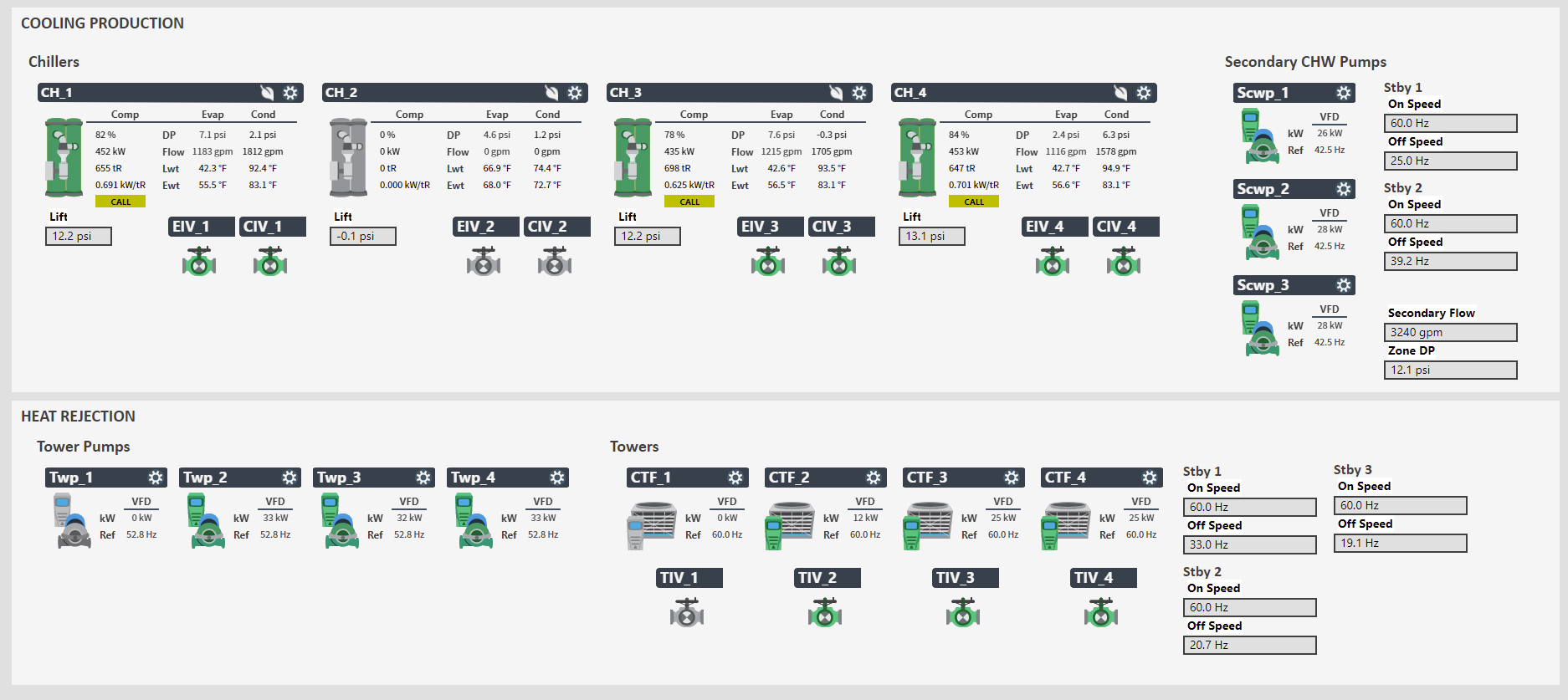
The university’s upgraded user interface enables operations staff to monitor individual equipment information and overall system parameters to ensure efficiency and reliability.
The first efficiency obstacle discussed was the chilled water plant’s primary/secondary hydronic design. Primary/secondary systems often suffer from “low delta-T (ΔT) syndrome,” a condition wherein cold water from the chiller and warm water from the load mix before returning to the chillers. This low ΔT reduces chiller capacity and places the chiller at a less-than-desirable point on its efficiency curve. With this reduced chiller capacity, the only way to meet the load is to turn on additional equipment, the net effect of which is that more equipment is operating and at less than design efficiencies. Further analysis revealed that a mix of constant-speed and variable-speed pumps were often in operation simultaneously, degrading efficiency and reducing pump redundancy. Lastly, the existing building automation system (BAS), which controlled all chilled water plant equipment, was in good working order but lacked an optimization sequence.
Upon reviewing these findings, university representatives agreed that a comprehensive chilled water plant optimization solution would be required to address the hydronic, mechanical, and control issues and to improve overall HVAC efficiency.
Hydronic: To eliminate the inherent mixing and raise the ΔT to design levels, an improved hydronic configuration was needed. While the variable/primary configuration is known to be the most efficient hydronic design, converting from a primary/secondary system is very capital-intensive due to the significant mechanical modifications required. The university team was able to implement an innovative solution that mimics the functionality of the variable/primary system but allows all existing pumps and piping to remain in place, simply adding a few sensors and valves for controllability.
Mechanical: The pragmatic conversion merely required the installation of differential pressure transmitters (DPTs) to monitor the flow on the evaporator barrel of each chiller.
Control & Optimization: The university required an efficiency solution that would ensure real‐time optimization of their chilled water systems. The chosen system utilized a supervisory architecture wherein it receives operating data from the existing BAS and the setpoints from the optimization algorithms are then sent to the BAS system for actual execution. These algorithms continuously adjust equipment operation and key setpoints based on such parameters as occupancy level and outdoor temperature to maximize the system efficiency in real‐time while maintaining comfort cooling needs.
The university’s new cooling optimization solution maximizes overall plant efficiency with the real-time determination of:
- Most efficient combination of available chillers needed to meet the cooling demand
- Quantity of chilled water pumps and condenser water pumps necessary to deliver the required volume of water at the lowest total power per unit of cooling production (kW/ton)
- Required chilled water loop flow parameters that will meet the cooling demand at the lowest power per unit of cooling production (kW/ton)
- Optimal chiller evaporator leaving water temperature sent to the building load based upon outdoor air conditions
- Equipment operating parameters that will produce the optimal condenser water temperature that will minimize total power consumed by the chiller and cooling towers
- Condenser water flow modifications to provide required heat rejection in the most efficient range of the chiller and with much less pump power (kW).
- Cooling tower sequencing to flow water over the maximum amount of cooling towers without falling below the minimum flow rate of the associated tower cells
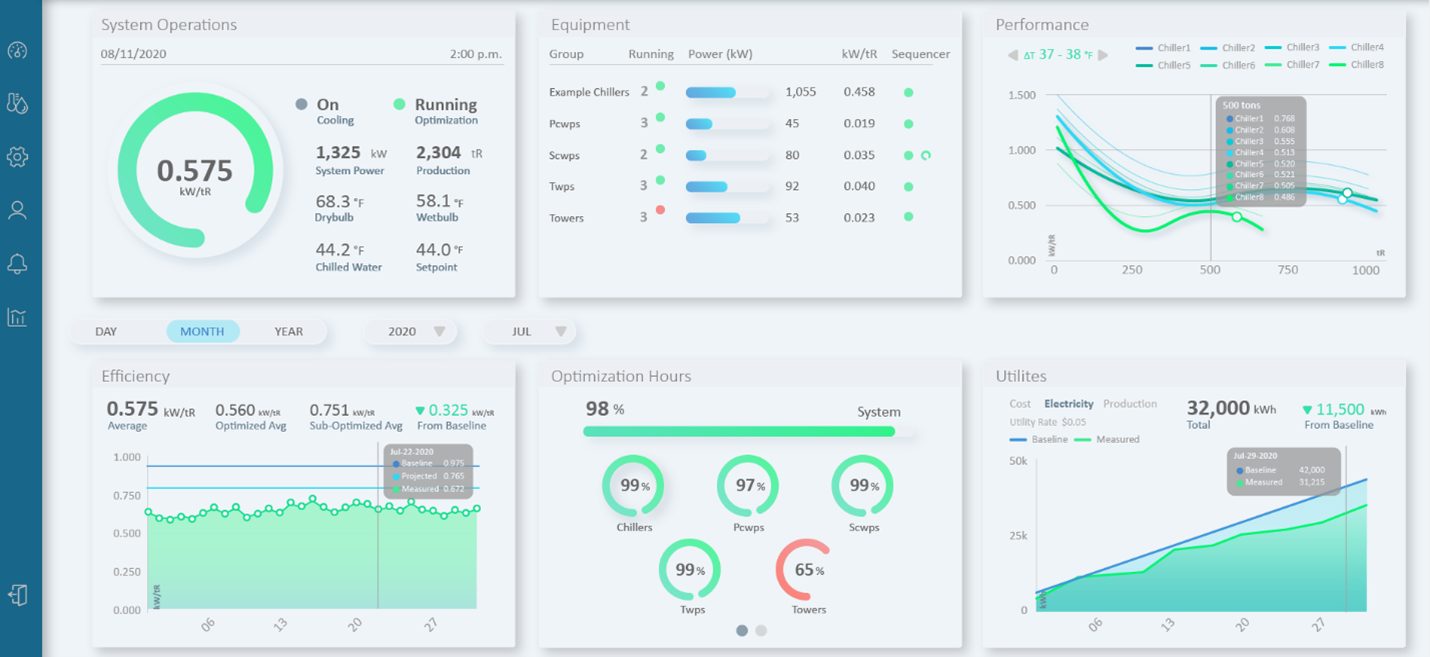
The university’s Energy-Efficiency Performance Dashboard delivers a window into the system, providing real-time and historical efficiency key performance indicators (KPIs) for troubleshooting performance-related issues and maintaining maximum system efficiency.
In addition to the adaptive optimization algorithms, the new system’s energy dashboard (pictured above) provides staff, operators, and management with a window into their impact on real-time and historical chilled water system energy performance. The dashboard allows the team to view each piece of major equipment’s kW and kW/ton performance as well as total chilled water system kW and kW/ton performance. In addition, a baseline versus actual graph shows real-time energy performance relative to historical data, while trending capabilities provide an instant look at the long‐term view of system performance.
Energy retrofits at the university have dramatically reduced energy consumption and cut maintenance costs, while also improving equipment lifetime and correcting deferred maintenance problems. The chilled water plant optimization project is no exception. In addition to significant energy savings, the system also provides the operations team with real-time energy data for all chilled water equipment. Understanding how energy is used can help quickly identify energy waste and equipment problems, as well as overcharges and errors on energy bills. Facilities and operations staff are also freed up for other tasks, increasing their bandwidth and response time. With the campus’s focus on becoming one of the most environmentally responsible colleges in the United States, the significant energy savings of this optimization project brings it one step closer to that goal.
Eddie Rogers is senior sales engineer at tekWorx in Cincinnati, OH. He can be reached at [email protected]. This is his first article for Facilities Manager.
Power Tools
Seeks to engage multiple voices from among FM ranks to bring fresh insight and real knowledge from the trenches on what’s working in planning and implementation for energy-related projects and innovations. To contribute, contact [email protected].
See all Power Tools.