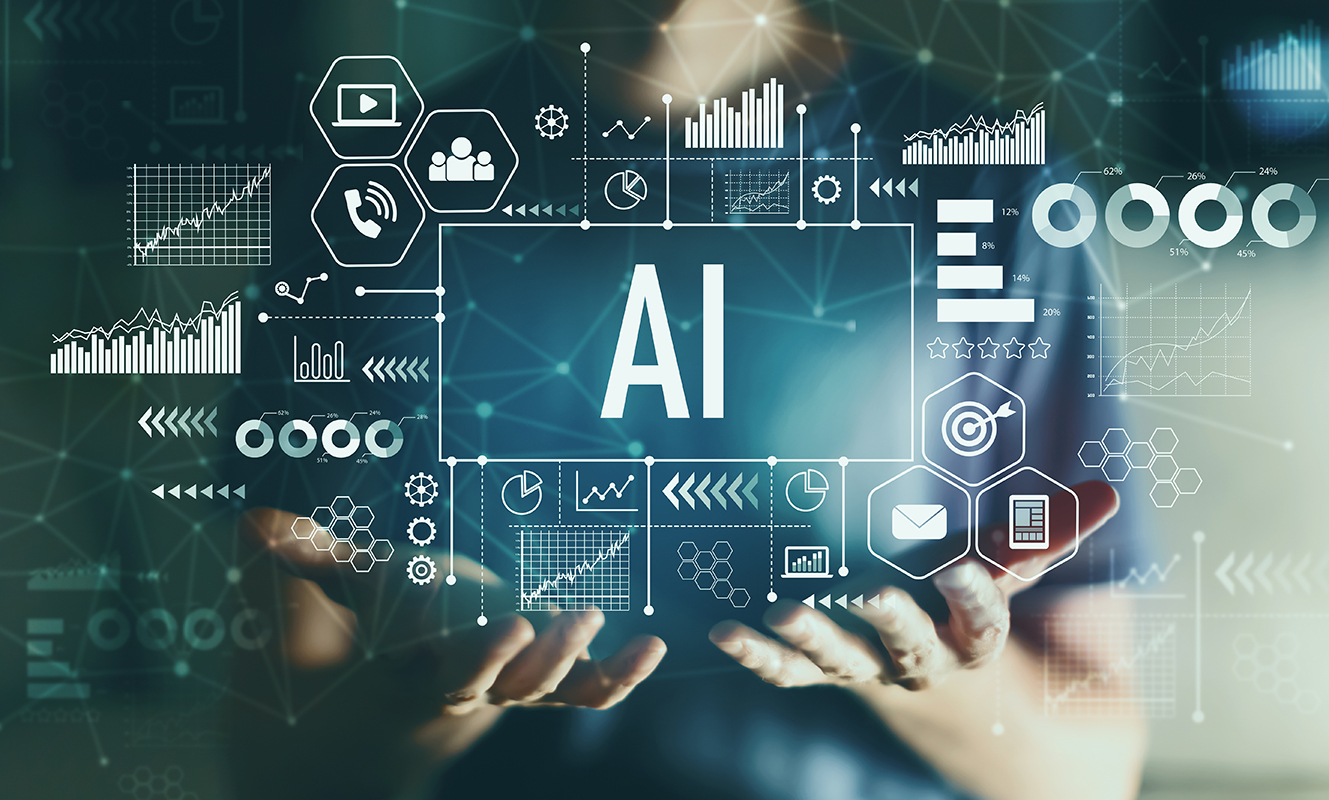
I was teaching APPA Supervisor’s Toolkit recently and suggested to the class that regenerative Artificial Intelligence (AI) had a role to play in our facilities organizations. Some were horrified, and others were excited to find ways it could be used. Afterward, I asked three people who I respect in facilities management (FM) what they see as the future of AI in their organizations:
Planning, Design, and Construction in Facilities: Heather Watenpaugh
Leveraging AI in facilities management will be transformative with new ways to improve and become more effective.
- Asset Management: AI can streamline the management of physical assets by automating inventory tracking, predicting maintenance needs, and optimizing resource allocation. Thus, capital managers can free up time to focus on aligning capital projects with strategic planning and better-informed solutions.
- Idea Generation and Design Assistance: AI tools can help generate design ideas based on input criteria, optimize floor plan layouts for space efficiencies, and conduct virtual simulations to test-fit scenarios during design development.
- Code Review and Compliance: AI algorithms can review building codes, regulations, and design guidelines throughout the planning and design phases, reducing the risk of costly errors and delays during construction.
- Construction Inspection and Quality Control: AI-powered drones, cameras, and sensors can inspect construction sites and detect defects or deviations from plans in real time, improving quality control processes.
- Training and Education: Facilities teams will need training to utilize AI tools effectively. Much of this includes understanding how to input data, interpret output, and integrate AI into the existing workflows. Having an internally designated “AI expert” can facilitate knowledge sharing and the adoption of new tools across the organization.
Business Services: Jeannie Knott
AI is about more than replacing human expertise. It is about augmenting those capabilities. Embracing AI technologies can lead to significant efficiency gains, enhanced decision-making, and improved outcomes in design and construction projects. By becoming and staying informed about advancements in AI capabilities, as well as collaborating with design professionals and construction partners, facilities managers will be able to create smart campus environments and streamline delivery. Like all efforts to optimize and improve processes and workflow, there are pros and cons to consider when discussing the integration of AI into (FM)’s business services.
The most obvious and commonly mentioned negative aspect of integrating AI would be the possible loss of jobs for those whose duties could ultimately be automated, or even predicted and implemented by AI. While this is not to say that this should prevent the use of AI in FM business, it must be carefully considered.
What must also be considered are the benefits that AI could bring to the business processes within FM. Imagine an AI recognizing an issue with an asset on campus, and then automatically creating a work order that would schedule service for our maintenance crews to provide. A process like this could significantly improve a preventative maintenance routine, as well as possibly reduce what may be added to a deferred maintenance plan.
Another aspect where AI could help would be in receiving vendor invoices and processing them through their applicable purchase order workflows, then billing them against relevant work orders in our IWMS. The AI could even flag invoices that do not match purchase orders, triggering a review process. FM buyers and accountants could focus their time on solving problems rather than any number of mundane entry and processing duties.
AI can help streamline FM’s business services and give our personnel the space to envision and move towards a future that allows us to optimally support our campus, students, staff and faculty, and community.
Plant Management: Ben Boslaugh
AI has the potential to be a valuable tool. Basic engineering principles have not changed, but how we apply them to campus HVAC and Utility Distribution systems has. The tolerances are tighter, as are the expectations of gained efficiencies. When we push the fan and pump curves; the cushion is smaller than has been in the past.
Self-tuning automation systems are not new. How well have our teams utilized them? Do you know which points you really need from a BACNet device or controller? One can easily be inundated with alarms and numbers (that have no real meaning). AI can be a tool to help sort thru the noise and leverage the instrumentation and automation already in place.
If appropriately utilized AI has the potential to help Central Steam or Distributed Chilled Water Plants run more efficiently. It could add data analytics that reinforce or challenge an operator’s intuition. Ask yourself, “How many times have operators placed overrides or adjusted a PID loop to “fix” a problem”? Only to find those “band-aids” still there months later. The most efficient system can be foiled by a lack of attention to detail or understanding.
AI cannot stand alone; it will never replace a well-trained operator. The maritime industry has wrestled with this for years. As AI grows, our teams’ education and training must grow with it. The question is, “Will AI make you more efficient, or will it learn your bad habits?”
Conclusion
It would be hard for anyone to say that cell phones, handheld devices, automated equipment, and other innovations have not made our jobs easier, so why would AI be different? How do you think AI will impact your area? Are you planning to learn about it, or will you just wait for it to happen?
Author’s note: We also asked CHATGPT to answer this question; for a copy of that article, please email [email protected].
Contributors
Heather Watenpaugh, AIA, is a registered architect working in the planning, design, & construction department of the University of New Mexico in Alburquerque, NM. She can be reached at [email protected].
Jeannie Knott is the assistant director of facilities support services for the facilities management department at The University of Texas at Dallas. She can be reached at [email protected].
Ben Boslaugh is the utilities manager in the facilities management office at Missouri State University in Springfield, MO. He can be reached at [email protected].
Glen Haubold is an APPA Fellow and Member Emeritus with years of service to APPA, CAPPA, and RMA. He can be reached at [email protected].
Power Tools
Seeks to engage multiple voices from among FM ranks to bring fresh insight and real knowledge from the trenches on what’s working in planning and implementation for energy-related projects and innovations. To contribute, contact [email protected].
See all Power Tools.