Campus utility master planning is a process to identify required utility services, strategies, and costs. Scope is based on a focused purpose, specific product, and periodic self-analysis to document existing utility systems, current needs, and the extent and timing of future needs. Master planning surveys organize data on institution utility systems and service needs, document conditions, develop strategies, articulate action plans, and communicate this information.
Why Master Planning Is Essential
The utilities master plan is a formal business and financial plan to address mission-critical utility service requirements (and avoid funding all utilities services because they are too critical to lose, incurring unnecessary inefficiencies and expenses). Building construction often is planned and budgeted without considering needed central plant and utility mains; systems are incongruent, have low first costs but high operational costs, or impose added operational costs and workloads. Facilities managers use the utility master plan tool (also used for planning and construction) to define utility and energy system needs and costs and to expand and maintain energy and utility systems. To avoid the physical and financial risks of informal and undocumented plans, the utility plan must be a written document (with communication and vetting processes) and must be integrated with campus-wide master planning and financial management. Formal planning supports development, analysis, and comparative testing of alternative utility systems; best practices to proactively address energy and facilities technologies; and balancing of life-cycle costs against non economic goals (e.g., sustainability, energy efficiency, transitional technology strategies).
Determine the Capability of Utility Systems to Serve a Growing Campus. A key utility master plan goal is assessing utility system capacity and service reliability (in relation to building sites and related costs) and identifying resource and capital investment requirements. Utility services costs for new buildings are reduced by advance planning, locating buildings near available service capacity, and prioritizing service capacity near growth areas. Independent variables affect new building sites (e.g., surplus central plant capacity, feasibility of decentralized utility facilities, utility services location and capacity, existing plant condition and age, cost and ease of adding capacity). Planning coordination supports provision of utility service capacity at a substantial cost savings. Utilities facilities condition assessments assess central and satellite plant capacity; distribution system capabilities; capacity expansion options; life-cycle cost of alternatives; utilities facilities (e.g., electrical, heating, cooling, and domestic hot water systems; sanitary and storm sewers; gas; telephone and communication systems); routing services methods (e.g., duct bank, tunnel, utility corridor, direct bury); load accommodation capacity; and needed improvements.
Determine the Magnitude, Cost, and Timing of Needed Campus Expansion. Another key utility master plan goal is anticipating demands on the utility system so that services are available when a new building comes online. Long-term strategic plans for central utility expansions often size capacity investments to meet several buildings’ needs, so timing must anticipate useful equipment life, reliability factors, capital constraints, and other issues. Planning for sector development over 5 to 10 years can save significant capital resources (e.g., for a new chiller or electric substation, a master plan can determine the magnitude of needed central plant and utility expansion, timing of the expansion, and required budget).
Determine Cost-Effective Ways to Meet Campus Expansion Needs. Master plans evaluate the most- cost-effective expansion options, but in long-term utility service planning, it is as much an economic art as engineering science. A central plant with many interdependent utility services is a complex economic system, with life-cycle cost performance depending on configuration of interrelated systems and external variables (e.g., energy prices). A utility master plan must document utility system performance, energy reduction opportunities, and future operating conditions based on observations of current systems. Assumptions about technology and service demand dictate utility infrastructure sustainability strategies. Integrated engineering and economic performance models produces more robust cost-effectiveness evaluations (e.g., net present value of system operations, such as debt, major maintenance, capital replacement, and operating costs for alternative facility configurations, alternative growth, and external factors).
Determine That Utility Systems Expansions Are Efficient in Meeting Expected Campus Needs. Good utility master planning mitigates improperly sized expansions that waste resources (e.g., when pipe runs must be duplicated or mains relocated), with disrupted building operations or out-of-service facilities. A utility master plan in the capital asset management planning context requires a physical assets inventory and analysis of condition, risk of capital asset failures (e.g., environmental safety, development priority changes), and fiscal strategies to maintain or improve assets.
When technologies change rapidly, risks and uncertainties must be formally addressed. A quantitative performance-model-based utility plan allows formal testing of assumptions about technology changes, uncertainties, risks, and future impacts.
Develop Institutional Support for Needed Expansion and Operations. Budgets for facilities operations and expansion are usually political or bureaucratic (not rational or good economics). If sponsored from day one by senior financial officers, utility master planning has a big advantage in securing required funding and support by assessing cash flow requirements to meet life-cycle debt, operational, and major maintenance costs.
Budgets and operations often rely on historic precedents (with adjustments based on economic trends such as inflation) and sometimes on square footage or student full-time equivalents. Short-term costs (e.g., reduction in current operating costs, lowest first-cost and first-year operating costs) can drive financial decisions, leading to deferral of renewal, modernization, and expansion; usually long-term utility system investments are particularly vulnerable. Effective capital asset management is a best practice and the foundation for sustainability in utility services planning.
Relation of Utility Master Planning to Overall Master Planning
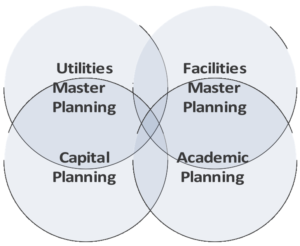
Figure 3.1. The Intersection of Master Planning
Facilities master planning addresses buildings needed to support the academic master plan; the utilities master plan supports both. All these master plans must be integrated. (1) The academic planning process defines academic programs, type of research, and number of students and physical requirements. The facilities planning process provides feedback on plant limits and improvement costs. (2) The facilities master plan defines square footage, remodeling, and replacements (and longer-term development and energy use targets) to support the academic plan. New building size and construction affect utility needs and operations and maintenance (O&M) costs. (3) Financial planning considers factors other than building and plant operating costs (e.g., academic salaries, administrative costs, economic risk factors, funding sources and methods).
The utility master plan gives financial planners information on energy and O&M costs and can incorporate in-depth business planning to produce data for the budget process (e.g., purchased energy, central plant operation costs, debt costs, distribution, custodial O&M) (see Figure 3.1).
Typical Elements of a Utility Master Plan Approaching master planning as a series of related steps while keeping the big picture in mind makes the process much more manageable (e.g., what exists; what is needed now and in the future; unmet needs and alternative options; feasibility, construction costs, and O&M costs of each option; best option and possible improvements; implementation strategies; schedule and budget; plan updates).
Existing Campus Assets. A current asset evaluation includes size or capacity, location, condition, and potentially useful hidden assets (examples in actual utility master plans include a hill above campus, gas under campus, roofs for solar installations, waste heat recovery options, waste paper, abandoned water reservoir, lake or wells on campus, nearby river or canal, existing utility tunnel or distribution systems, utility company incentives, utility net metering, incentives for conservation and load management).
Existing Campus Liabilities. Liabilities (many the result of past inadequate planning) are easy to find but difficult to convert to assets or at least neutralize. Examples of liabilities in actual master plans are poor or trapped central plant location; inadequate distribution for expansion; failing central plant or distribution mains; air emission constraints; systems, distribution, or equipment that is deteriorating, undersized, or unsuited to current technology; and inefficient plant or utilities with remaining useful life.
Current Energy Loads, Location, and Uses. A key utilities master planning element is analyzing energy use records (e.g., how much, what type, sometimes where) and comparing to use at similar institutions. Other useful data include peak load and energy time-of-use consumption patterns (e.g., via advanced metering, smart grid management, energy management software, and sometimes electric utility records). Facilities management strategies increasingly depend on energy use data (e.g., individual building use patterns, required transport energy). Potential economic benefits in facilities management and utilities services planning are likely to drive larger investments in metering and monitoring systems and dashboards.
Expansion and Replacement Needs and Schedule
Master utilities planning (and capacity increases or other modifications in energy and utilities) is based on future loads, using academic and facilities master plan projections (e.g., building types, sizes, uses, sites, needed remodeling or replacement, expansion schedule). Using the loads, design concepts are identified; rough-sized equipment is selected; modification or expansion sites are defined; and costs are estimated. For new or extended systems, utility installations must be flexible (e.g., responding to changing energy costs, service availability, technology advances, expansion needs), but budgetary constraints seldom allow large expenditures far in advance of future growth, so significant input is needed from the most knowledgeable available utilities experts (often as part of the self-evaluation). Project timing must factor in (often unusually) long lead times and avoidance of multiple independent construction projects.
Potential Solutions: Central vs. Individual Building. One typical evaluation in university master planning is a comparison of the relative merits of stand-alone (local site) solutions versus central campus system. First- outlay, energy, and operation costs can be compared relatively easily, but some variables are more difficult to identify and quantify.
Current Available Energy Sources and Systems Cost. Utilities master plans consider energy sources and costs (including cost of related systems). All potential energy sources and costs should be thoroughly evaluated (e.g., electricity, natural gas, heat recovery, geothermal, oil, wind, solar, coal, biomass, liquid biofuels, solid waste).
Integrated Energy Solutions
The most effective university energy solution uses the principle of synergy (e.g., thermal storage, heat recovery, cogeneration, energy use reduction, variable volume systems). The utilities master plan develops the best integrated long-range energy solution for a specific campus (often a unique integration, not the product of cookbook engineering), using each energy source to its best technical and economic advantage (considering cost, reliability, and flexibility). (See figure 3.2.)
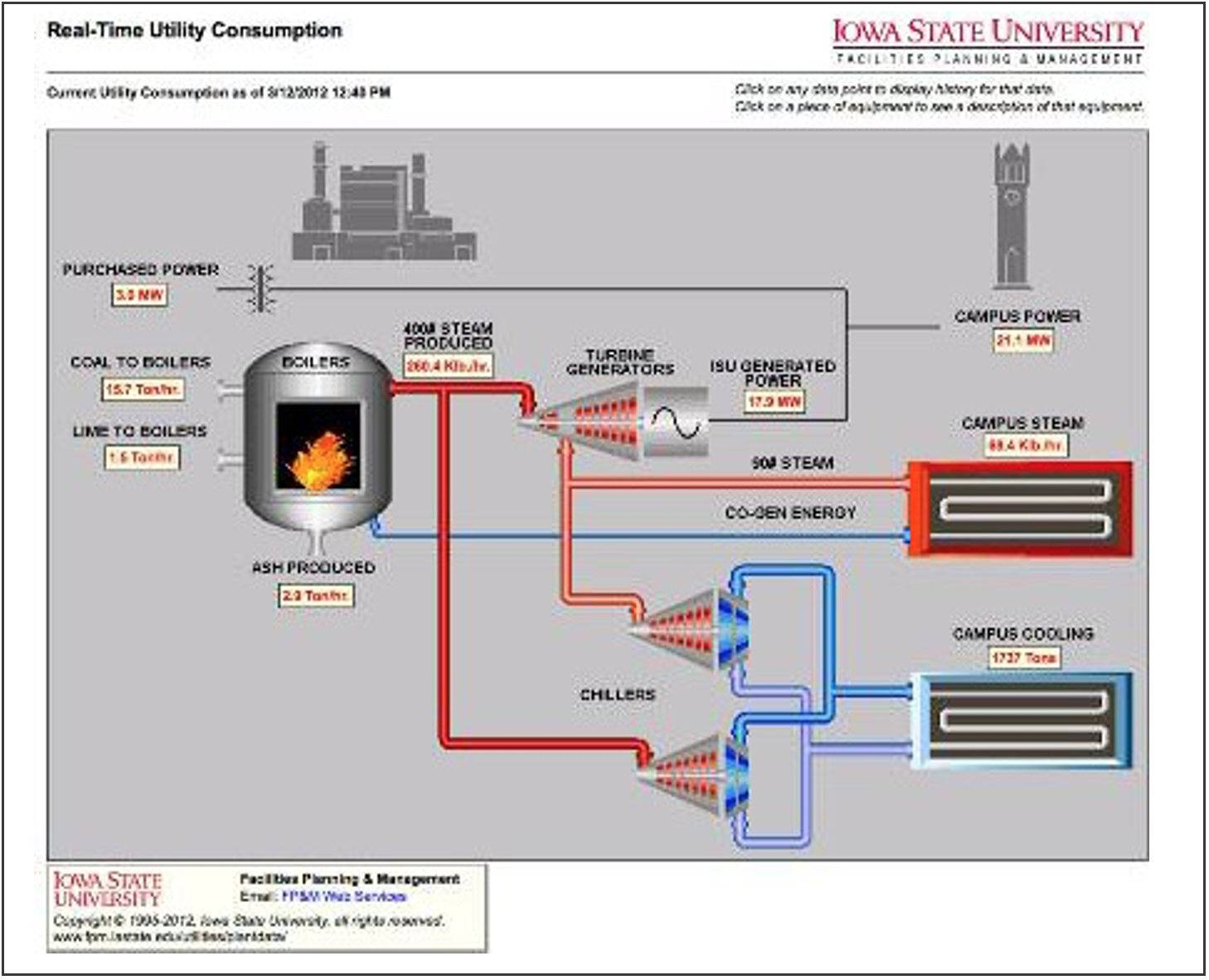
Figure 3.2. Real-Time Consumption/Iowa State University Cogen System
Primary Campus Energy Production Options. Viable integrated energy combinations used on previous projects include (1) chillers with heat recovery (improving heating and cooling efficiency); (2) boilers with heat recovery (recovering half or more of the 20 to 25 percent of fossil fuel energy waste in hot stack gases); (3) thermal storage (generating energy at one time and using it later); (4) solar (passive or active, becoming a significant energy resource, with big cost- effectiveness improvements and noneconomic factors, such as sustainability and renewable energy goals); (5) geothermal (providing heat or cooling, regardless of source temperature); (6) biomass or waste-energy- containing materials (eliminating new energy purchases while processing solid waste, but with key air pollution controls and ash disposal issues; likely to become a significant energy source); (7) nearby industrial waste heat; and (8) free cooling concepts (using cool geothermal, for example).
Potential Solutions to Meet Changing Conditions. Change occurs, and most specific predictions are wrong. Campus utilities master plans analyze technology risks and consider effects of, and responses to, changing conditions. (1) Short-term energy costs can rise or fall (but real costs rose less than the general inflation rate for the last 30 years). Utilities master plans analyze energy price risks (e.g., sustainability impacts) and the role and life cycle of technology-specific incentives (e.g., net metering). The best energy solutions shift with energy economics and other metrics (e.g., conservation, carbon reduction, renewable energy strategies). (2) If a fuel type might be unavailable (or unacceptably costly or too environmentally damaging), a backup fuel system is needed. Complex master utilities services plans include strategies to enable fuel switching or requirement changes (e.g., at energy system end of useful life). (3) Indoor environment requirements change because of changes in building occupancy and environmental regulations (e.g., stronger ASHRAE outside air requirements for new and remodeled buildings; changes in acceptable temperature or humidity), so central energy systems build in flexibility. (4) Central plant locations (e.g., physical centrality, accessibility) affect operation and expansion costs and delivery. In master plans, distance incurs both first-cost and life-cycle operation cost penalties.
Campus growth plans integrate central plant site based on logical development, academic access, smoke, cooling tower plume, winds, noise, and vibration. Central plant site affects operating efficiency (e.g., load proximity, service access, outside utilities location, O&M labor cost).
Major Variables Affecting Master Planning
Many variables (campus-specific factors aside) have a major impact on systems. (1) Energy costs and system efficiency are not always directly related. Cost is not always the key issue (e.g., heat recovery for hazardous waste disposal; cogeneration for plant reliability and emergency performance). A system can become more inefficient over time, with poor maintenance, or in response to energy costs. (2) Labor cost and equipment maintenance are part of system life-cycle costs and vary with specialized maintenance, more maintenance, and high-cost replacement parts. (3) Building systems and interface requirements are part of conversion costs for energy central plants and distribution systems (e.g., piping and coil changes, main piping interfaces to buildings). (4) System size and capacity are the starting point for planning. Delivery system capacity often can be determined only by computer modeling or system stress tests. (5) Campus diversity factors (i.e., a peak load for each major energy system that is almost always less than the total of all building peak loads) allows slightly smaller sizing of heating and cooling systems.
Diversity factors are difficult to calculate (e.g., if available, comparison of sum of calculated peak building loads to measured peak use; seldom-used campus computer models; usually conservative engineering experience factors). The load profile (i.e., measured load as it varies across a day, week, month, or year) helps predict overall system performance and average efficiency. (6) Thermal water system designs use supply and return temperature differences (the greater the difference, the more capacity delivered for a volume of water). Steam pressure designs typically use a gross estimate of needed pressure, showing little correlation among design, operation, and need. Design and operation of steam systems (or high-pressure water systems) at temperatures higher than needed result in significant energy waste and often increased labor costs. Water delivery system operation and metrics offer insights into campus systems. Data on heating and cooling temperature differences are needed (combined with flow rates) to assess system effectiveness, possible increases in capacity, and needed remedial measures. (7) Probable developments in energy sources require projections of availability and price for incorporation in long-range planning.
Solving the Economic Dilemma
Facilities managers face the continual issue of low first costs or low operating costs; versus life-cycle costs, capital asset management data (e.g., financing, energy, maintenance, replacement costs; salvage value), and net present value of alternative investments. (1) Higher first cost versus higher operation and maintenance costs.
Central plant systems have higher first costs, longer lives, centralized maintenance, and low new system hookup costs. Local site solutions have lower first costs but higher operation costs. (2) Staying the course.
Implementing a long-term utilities master plan depends first (and foremost) on its adoption as a business plan and then on dynamic planing interim testing. Costly master plan updates are not made in response to each new building or option. (3) Resisting the temptation of low first cost. This is the most common reason for attempts to deviate from the plan (user needs versus tight budgets). (4) Evaluation of deviations from adopted master plan. Each deviation must be fully evaluated, using a formal (adopted and enforced) procedure. (5) Keeping plan up to date. The dynamic plan should be updated every 3 to 5 years, responding to campus growth and conditions, information technology changes (e.g., distributed metering), and trigger events (e.g., new information on major building needs, including computer model data; tracking of actual utility use, operation costs, and trends versus simulation model projections; and major changes in equipment, energy use or cost, or availability).
Leave a Reply
You must be logged in to post a comment.