In educational facilities management, work management matches customer needs with resources to provide the optimum physical environment for instruction, research, and public service.
Work Management Information
Work management converts customer (e.g., faculty, staff, students, police, security, and visitors) concept into data to define achievable tasks. The service desk (or assigned staff) interacts with customers, assigns a unique work order number, gathers core data, updates data, and approves and assigns work; this process can be simple (e.g., replace light bulb) or iterative (e.g., design and build hospital). Work order key data elements include work order number, emergency flag field (for imminent threats to people or property requiring immediate response), requester (point of contact), location (e.g., Postsecondary Education Facilities Inventory Classification Manual space classification; building number; geolocation); scope and feedback expectations; status (e.g., changes, by whom, and when); fund provider and identifier (e.g., billing as recorded or cyclical billing; shared costs); budget expectation; and desired (non specific) schedule of completion. Authorization and assignment begins with needed permissions, which vary but can be tied to expenditures, institution priority, work nature, and location. Fewer permissions mean a more efficient work order process. A work order empowers a work group to proceed under current permissions and is issued by the service desk, work group supervisor, or scheduler, depending on organization structure (e.g., trade-based or central shop, zone-based, function-based, hybrid). Work assignments are recorded, communicated clearly, and coordinated among multiple work groups if needed.
Every work order indicates who, what, when, and where and feeds organization-specific business processes (e.g., work order timestamps; log of changes by whom and when; work type by major type and subcategories; primary trade; required permits as recorded in work order or permit system linked to work order system; notifications (e.g., planned outages, architectural review); project parent-child relationships; priority (if not obvious); and expenses (e.g., time, material, equipment) to enable billing and answer any questions.
Cost Estimating
Customers usually need to know project costs before authorizing work. Work management collaborates with customers and facilities staff to provide cost information based on pricing agreement type, such as (1) time-and- material (agreed-upon scope and order of magnitude, large cost swings unlikely, time better spent on work, funder bearing overrun risks), (2) fixed-price (hard funding limit, well-defined scope, detailed cost estimate, service provider bearing overrun risks), (3) guaranteed maximum price (fund and service providers cooperating to minimize costs and share overrun risks and sometimes enable savings), and (4) unit rate (detailed rate list, used with other pricing agreements to address uncertainty); and (5) estimate type, with detailed data supporting simple- addition estimates (supported by consultants and resources such as RSMeans) and lack of data leading to order-of-magnitude estimates (e.g., based on price per square foot, historical costs of similar projects, or RSMeans). The estimator needs facilities management experience, work site and institution knowledge, and capability to judge the impact of project constraints.
Scheduling
The work management group usually performs master scheduling (e.g., understanding each group’s services, backlogs, available contract resources, lead times, available equipment), assigns work to a group, and collaborates with work units and customers to refine delivery schedule. Many facilities management products are custom and require investigation, planning, and estimation, but many are repetitive and predictable (e.g., custodial and grounds services, preventive maintenance). Management seeks ways to shift unplanned work to planned work to improve efficiency and emergency responses, set completion expectations in advance, and reflect institution priorities.
Expectations should be set (e.g., defined response times) and communicated to customers to facilitate management and fewer surprises. Front-line supervisors make or affect daily staffing decisions, with individual work assignments made throughout each day or allocated daily or weekly.
Work Control
Work control is routine and ad hoc planning, measurement, follow-up, and reporting on work. Planning reviews work backlogs, resource availability, and issues such as utillizing an institutional calendar to estimate work completion dates and guide work assignments. Work control can measure performance at many levels (e.g., actual costs, percentage of preventive maintenance work orders completed on time, estimated versus actual preventive maintenance work-hours, time to complete emergency work order, etc.). Major projects can merit a summary report (e.g., percent complete, planned versus actual costs and schedule, issues). Such data should be captured in the work management system. Work management tends to be associated with certain business functions (e.g., customer service and maintenance program management) that address institutional appearance, which is important in attracting students, faculty and staff. Proactive customer relations and customer communications are key to a positive impression, which makes work easier.
Customer Communications
The Internet enables facilities management organizations to make an electronic impression on customers via websites, online service guides, automated status updates, outage notifications, service bulletins, annual reports, and newsletters that are customer focused and aligned with institution mission and goals.
Customer Relations. The customer service group usually has the reactive job of answering customer phone calls, online requests, and email; it is the de facto voice if not the face of facilities management. Even though they devote spare time to other duties, customer service personnel need to be available to customers.
Proactive customer relations programs initiate and nurture customer interactions (especially at large schools where building users are more disconnected from staff). Facilities management can connect with the school community in many ways (e.g., full-time customer relations manager who regularly visits key department contacts to build rapport and trust, facilitate communication and coordination, and who serve as customer advocate; facility coordinators who identify key department personnel who interact most frequently with facilities management; creation of a facilities management advisory board; and customer feedback solicited via short and relevant surveys and used to reduce the chance of a problem recurring).
Maintenance Operations and Program Management
Maintenance and operations management (i.e., systematic maintenance and upkeep of facilities, grounds, infrastructure) and program management (i.e., process of applying details to specific school) focus on securing resources and deciding how to use them.
Grounds care, custodial services, and maintenance programs require management with technical and operational details specific to the discipline, levels of care, and staffing metrics. This systematic approach begins before new facility concept, with financial realities of owning buildings, land, and infrastructure (e.g., one approach has maintenance endowment equal to building construction costs). The Maintenance Reinvestment Rate (MRR), Annual Repair and Maintenance [M&R] value divided by current replacement value [CRV]) and the facility condition index (FCI, estimated cost of M&R to return buildings to original design performance, or maintenance backlog, divided by CRV) are simple and integral to maintenance program management and investing to maintain asset value. The National Research Council concluded that M&R should average 2 to 4 percent of current inventory replacement value (if no backlog). An FCI of less than 5 percent indicates few maintenance needs, and 5 to 10 percent indicates occasional issues with usually acceptable impacts, but more than10 percent means recurring problems in one or more systems, with noticeable occupant impacts. The common denominator of MRR and FCI is CRV, which must be carefully selected, used for many years, adjusted for inflation, and updated. CRV improves FCI and worsens MRR; FCI commonly updates both numerator and denominator with the same inflation index (so adjusted FCI is functionally unchanged), but the MRR numerator (M&R budget) does not increase with inflation and might decline because of other budget forces. To overcome the challenge of stabilizing budgets given competing priorities, presentations should include pictures of maintenance deficiencies, estimated unfunded repair costs, needed funding to achieve 5 percent FCI, and future backlog projections based on varying funding levels. When funding is secured, maintenance program managers in different organizations must collaborate as a single work group with integrated goals. Disciplined expenditure decisions depend on considering mission and needs, different ways to meet them, resource allocation plan (financial budget, with expectations and frequencies recorded in multiple uses), feedback, final general and specific plans (available to university community, work authorization, monitoring of execution compared to plan), and plan refinement. The resource allocation plan is a useful reference. Maintenance resources can be allocated to blend the mix to align with institution priorities and long-term facility portfolio health but must include facility condition assessments and maintenance.
Facility Condition Assessment Program Ongoing facility condition assessment programs contribute invaluable data to the resource expenditure decision process and begin with a facility inventory of each building and its rooms, including name and identification number, occupancy date, gross area, replacement value, physical location (address, room number and area), station count, room use, and
department assigned the room. Less common but ideal is tracking this information for each infrastructure system. The deficiencies for each facility are captured and recorded (e.g., identification number, description, building system, estimated repair cost, priority, status). Full condition assessments cost more but are best utilized to create detailed, prioritized, and categorized deficiency lists based on site visit inspections and planned actions. The less expensive probability-based life-cycle option uses a site visit to document building numbers and types and inspector estimates of remaining useful life as input for a software application that calculates building condition and estimates cost (based on unit rate); it offers a quick and general picture of backlog value and possible problem areas but suffers from lack of specificity and uncertainty as to whether the need is real or calculated. Numerous contractors provide both types of assessments and related databases and software; institutions can use contractors, in-house staff, or both. Inspection frequency is every 4 to 5 years, with intervening updates. The facility condition database can record non- maintenance building needs. If every appropriate improvement is captured, all needs divided by CRV equals renewal requirements index (useful for capital planning).
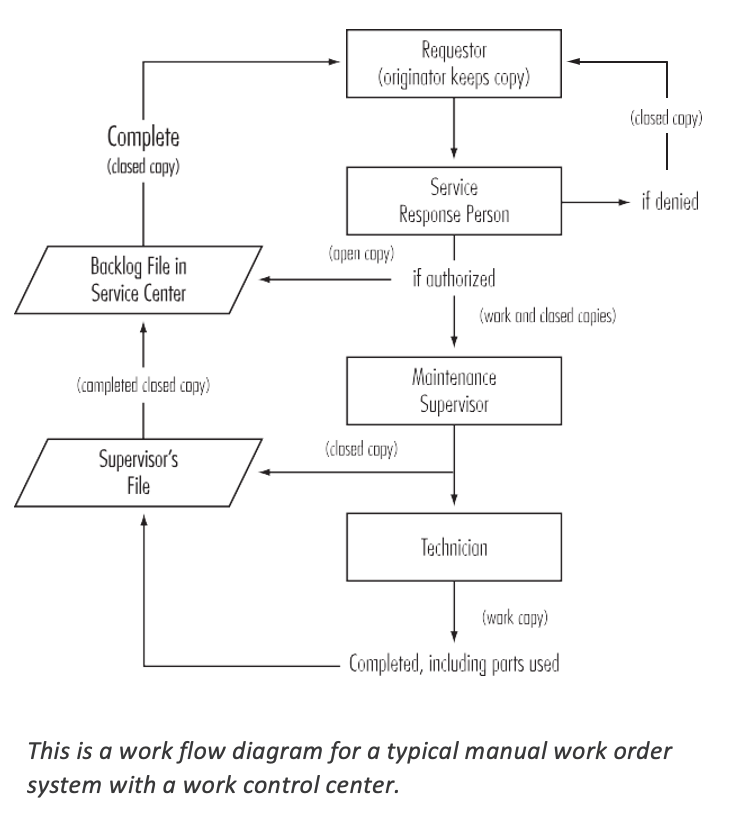
Figure 2.11. Manual Work Order Flow Diagram
Source: APPA’s Operational Guidelines for Educational Facilities: Maintenance
Maintenance Program
Maintenance preserves assets for intended use and enhances appearance, reduces noise, and minimizes interruptions. The implied objective is cost-effective maintenance resulting in lower operating costs. Subtle changes can reduce operating and maintenance costs. Preventive maintenance focuses on planning; objectives include reducing breakdowns, documenting legally required work, and reducing energy consumption and overall maintenance costs. Computerized Maintenance Management Systems (CMMS) can automatically issue preventive maintenance work orders based on elapsed time, with maintenance frequency defined and adjusted over time based on malfunction impacts, manufacturer and in-house staff recommendations, operating environment, safety and code requirements, equipment age and condition, and available staff and funding.
Software can project (and optionally level out) workloads for each department, such as predictive maintenance (based on ongoing measurements or an event rather than elapsed time), painting, corrective maintenance (minimized unless run-to-failure), major maintenance (expensive enough to require review and priority process), capital renewal (5 to 10 years before age affects performance of even well-maintained buildings), maintenance measurements (core and variable feedback metrics such as FCI, maintenance investment rate, APPA’s Facility Performance Indicators), and system audits (independent measurements, useful for critical systems). (See Figures 2.11 and 2.12.)
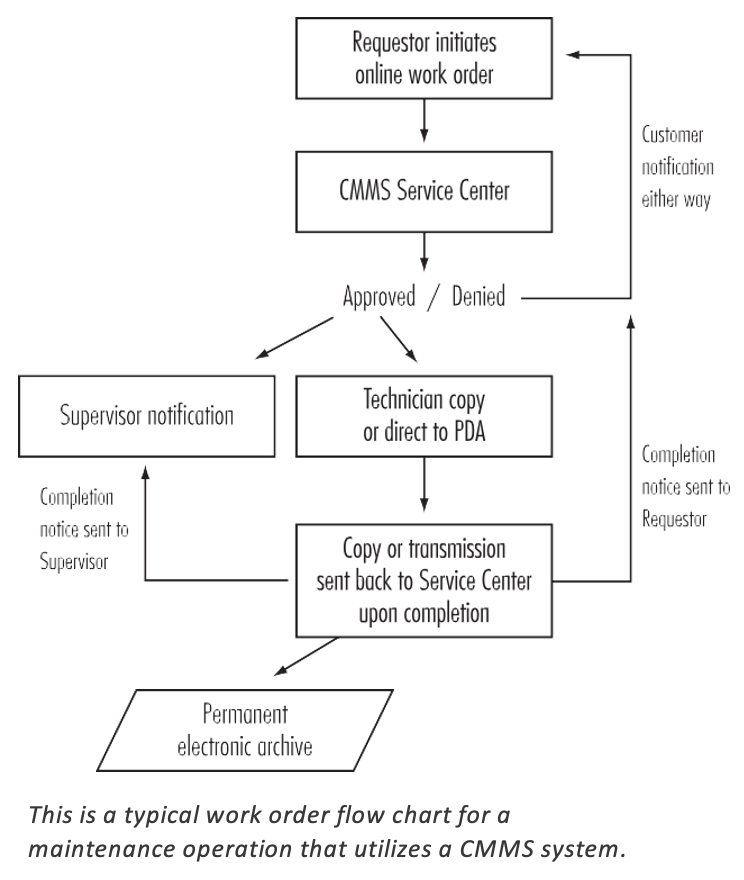
Figure 2.12. CMMS Work Order Flow Diagram
Source: APPA’s Operational Guidelines for Educational Facilities: Maintenance
Leave a Reply
You must be logged in to post a comment.