Building mechanical systems provide an environment that protects the building structure, creates safe and healthy surroundings, and allows equipment to operate properly. This chapter details how mechanical systems work and their comparative advantages and disadvantages, costs, and maintenance needs.
Design Considerations
General Considerations. Mechanical system selection and design are an optimization process, balancing the top goal of meeting program needs with design issues (e.g., functions, costs, aesthetics, energy use).
Building Functions. Mechanical systems should fit building functional use (or architectural program, in design phase); systems operate only as needed (e.g., when facility is unoccupied, optimal protection for contents, optimum energy to return to service). Special conditions (e.g., fume hoods, computers, clean rooms, animal rooms) must be analyzed early in the design process. Codes, standards, and common practices, balanced with user desires, dictate selection, design, installation, and operating needs. HVAC meets environmental needs (e.g., humidity, tight tolerances); and while not all features are always needed, once equipment is installed, operating characteristics are not easily changed. An energy- efficient HVAC system is more likely to occur with engineering input (e.g., space, function locations) during architectural design.
Budget Considerations. Short-term and mostly cost- related budget issues can dictate mechanical system selection and design to the detriment of future operational and maintenance costs. For early budget planning, available mechanical system options and life- cycle costs over building life must be understood (e.g., separate systems, larger systems that can be divided into zones or subsystems in the future). Budget concerns cannot compromise critical environmental controls (e.g., medical or research facilities).
System Zoning. Specific zones have individual control over space environments via a separate system for each zone (or a large system providing specific areas of separate control). Several separate systems can provide additional zoning to specific areas in the gross area served by each separate system. Minimum basic zoning is mandatory but must be balanced against cost and unnecessary maintenance of excessive zoning. Zoning types include (1) basic zones, determined by weather, especially solar effect (with perimeter and interior zones); (2) functional zones that group spaces with the same exterior exposure or interior zone function (e.g., offices, classrooms, common areas, auditoriums, computer rooms), with no (or only a few) spaces in a zone differing significantly in temperature, air purity, humidity, or hours of operation; and (3) time zones, which can economically provide separate systems for separate building functions with different hours of operation (often three time zones), with the digital control option to tie occupancy sensors to heating and cooling and lighting systems.
Architectural Considerations
Restricted mechanical space (e.g., because of maximum usable space, aesthetic concerns) imposes little understood and often neglected costs during construction, installation, maintenance, modifications, and replacements. Mechanical systems must suit the building functionally, with ample access for installation (e.g., ducts, pipes, terminal units, ceiling space, shafts), modification, maintenance, and replacement; architectural designs and field-built air-handling units can improve access. Building site (e.g., location, orientation) affects mechanical system selection, sizing, and placement. Outside air intakes and exhaust systems must be separated (e.g., avoiding loading docks, planning for wind effects) to address air quality.
Aesthetics. Mechanical systems affect building architecture (e.g., air grilles, fume hood exhaust stacks; functional layout needs; specialty systems; surface materials durability review based on exhaust streams). Mechanical system selection and layout can minimize aesthetic impacts if integrated into early designs.
Heating-Cooling Source. Sources can be in the building or a central plant. Some mechanical systems demand the former (e.g., evaporative cooling, packaged heat pumps or unitary equipment).
Noise and Vibration. Noise and vibration can interfere with functional use; control is a team effort (e.g., department occupying the space, architects, structural engineers, mechanical engineers) to reduce costs and attenuate noise through equipment selection and mass. Noise criteria levels for spaces might not match facility needs. Component and system selection and sizing play a key role in resulting sound levels, which are difficult and expensive to change once built into the system.
Human Thermal Comfort
To be comfortable, people must attain thermal neutrality. Research across age, sex, and nationality has produced similar results on the seven factors (four environmental, two adaptive, one stress related; each described briefly) that affect thermal comfort: (1) air temperature (convective and respiratory heat loss); (2) relative humidity (heat loss via perspiration and respiration); (3) air velocity (cooling); (4) mean radiant temperature (net energy exchange between human body and surrounding surfaces); (5) clothing level (variable insulation level, measured by clo); (6) activity level (variable, measured by metabolic equivalents, or mets); and (7) time, when people move from the comfort zone to a stressful condition (i.e., the body expends energy to adapt and maintain temperature but cannot do so for long without stress), measured by a heat stress index (e.g., wet bulb- globe temperature, endorsed by NIOSH, or Belding and Hatch Index) or cold index (e.g., Belding and Hatch).
Ideal conditions are 76°F, 50 percent relative humidity, 50 fpm air velocity, mean radiant temperature equal to air temperature, clothing level of 0.6 clo, and activity level of 1.0 met; even then, 5 percent of people are not satisfied because of metabolism. This chapter and examples explain the relation of these variables to air temperature (Figure 2.19, for use in determining condition equivalency) and the thermal comfort envelope for air temperature and relative humidity ranges (other variables held constant, with a notable range from summer to winter).
Figure 2.19. Human Thermal Comfort Variable Relationship
Ventilation
Ventilation protects occupants (the focus of this section) and the facility. Indoor air pollution is controlled in three fundamental ways (i.e., removing the source, providing sufficient ventilation air, masking odor). This section focuses on proper system design for ventilation (used by most educational facilities).
Ventilation Requirements. Ventilation requires the correct amount and delivery of clean air. In an air- handling system, ventilation rates refer to outdoor air (makeup air); outdoor and recirculated air are combined to create mixed air, which is filtered to become ventilation air, then heated or cooled to create supply air. ASHRAE Standard 62 initially required large amounts of outdoor air ventilation rates; but during the 1970s energy crisis, Standard 90 specified meeting ventilation requirements with minimum ventilation rates (and thus minimal outdoor air). The current Standard 62 accounts for both building and occupant impacts on ventilation needs; the new calculation is much less than the old standard. Many factors (e.g., operating rooms, animal housing, laboratories) require special attention, especially during design, when relevant standards and regulations should be consulted. The design engineer must create a system that delivers proper amounts of outdoor air to meet clean air needs over a full range of operating conditions.
Ventilation Delivery. Manufacturers of supply air diffusers and grilles engineer the throw and drop of supply air devices to ensure good ventilation efficiency, the ratio of supply air that reaches the occupied area of space divided by total supply air introduced into the space. Engineering studies show that a grille or diffuser can provide the right throw and drop so that supply air is introduced with enough velocity to force it down into the occupied area but not enough velocity to create drafts.
Certain heating and cooling systems (e.g., variable air volume [VAV] systems) can affect the proper operation of grilles and diffusers and the throw and drop; one solution is an induction or fan-powered VAV box.
Indoor Air Quality. Basic indoor air problem categories are: (1) building-related illness from bacteria and viruses growing in building systems (e.g., Legionnaire’s disease), alleviated by proper maintenance and cleaning; and (2) sick building syndrome, a poorly understood problem apparently (according to general consensus) the compounded result of more energy-efficient buildings, inattention to air-handling system design, and reduced maintenance because of budget cuts, with some evidence that individual pollutants below guideline levels can produce synergistic effects. Another problem is the introduction of new pollution sources (e.g., furniture, carpet, printers, copiers) in the space with no attention to ventilation. Point source pollutants can be addressed via a local exhaust system or replacement with alternative products (e.g., LEED-recommended non- or low-VOC construction materials). Air-handling systems must be designed, installed, and properly maintained to avoid air pollution problems.
Filters. Filters are an important part of a quality air system and can reduce energy use and improve air recirculation. The almost endless filter choices (e.g., high-efficiency particulate, chemical-type, carbon, electrostatic) are disposable or permanent, with varying degrees of efficiency, costs, and advantages. Filters should be only as efficient as required because of installation and maintenance costs. All high-efficiency filters should be downstream from lower-cost roughing filters, which serve as pre-filters. MERV filter ratings indicate the capability of specific filters to remove different size particles.
Building Central Plant Systems
Heating Source Components. Selection of a building heat source is usually based on the building budget, energy costs, history of previous success, and institution preferences.
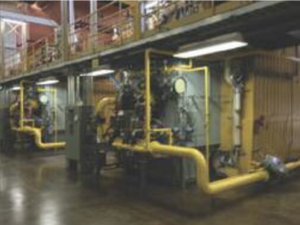
Figure 2.20. Image of a Boiler
Types of Boilers. This section briefly describes how boiler types work and their uses. (1) Steam boilers require careful monitoring, water treatment, and periodic blowouts (with fire tube boilers most common, and cast iron sectional boilers less so, in average building steam heating systems). (2) Hot water boilers (in the same models and configurations as steam boilers) are popular in this country (in many cases, codes do not require a boiler operator at all times). Operating at too low a water temperature causes corrosion, so temperature variation is achieved by blending valves. Pulse-type combustion burners have led to high-efficiency hot water boilers (unmatched by steam boilers). (3) Cast iron sectional boilers are used for steam or hot water and are highly resistant to corrosion but can crack under thermal shock (avoidable via careful design). They require relatively little floor space, with initial cost comparable to that for a fire tube boiler, and can be field assembled to replace relatively inaccessible boilers. (4) Modular boilers use many small boilers, each operating at full load in sequence, vastly improving seasonal efficiency.
If some boilers never come online, they can still provide standby capacity and support added load in the future. Modular boilers are widely applied in steam and hot water systems, reducing energy use by as much as 30 percent. Multiple boilers in central heating plants usually operate in modular mode. (5) Electric boilers (steam or hot water) depend on costly electricity from nonrenewable resources, but boilers that later can be switched out are better than electric heating units throughout the building. Sometimes a supplemental electric boiler can improve overall efficiency (e.g., cogeneration). Electric boiler heating elements deteriorate because of mineral deposits, but sheathing or enclosing the elements can resolve the problem (see Figure 2.20).
Heat Pumps. One or more heat pumps can be a flexible heat source. Small modular heat pumps can be relatively economical and low in initial cost. Size limits, maintenance in multiple locations, and noise can be constraints. Heat pumps are used in small facilities (one or two zones) and ground source applications.
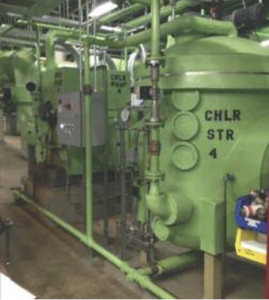
Figure 2.20. Image of a Chiller
Cooling Source Components
Air conditioning is now the standard expectation for people and activities (e.g., computer rooms, medical and research facilities). Current cooling sources vary in mechanical device complexity (e.g., design, operation, maintenance, energy sources). Low initial cost is important, but energy costs are a major selection factor. Refrigeration systems typically use CFCs and HCFCs (including R-123 but not R-134a), which are being phased out by international law (see Figure 2.21).
Direct Expansion Systems
One of the oldest and most popular refrigeration systems, a direct expansion refrigeration cycle achieves its cooling effect by expanding liquid refrigerant into a gas and often has a reversing valve to act as a heat pump. This section explains the function, advantages, and costs of options. (1) Reciprocating compressor chiller are piston-type and typically package components that use a water-cooled condenser or remote air-cooled condenser. They range up to 200 tons; are mostly electrically driven; are hermetic, semi-hermetic, or closed; and have solid-state controls for monitoring and diagnostics. They tend to be noisy, use more energy (reduced by improved design), and can last 20 to 25 years. (2) Screw-type chillers, a compressor type that operates with direct expansion or chilled water systems, can be cooled by air or water and range from 40 to 800 tons. They are very quiet, have fewer moving parts, and are competitive with reciprocating and centrifugal chillers (80 to 150 tons). (3) Centrifugal chillers use single, dual, or multiple compressors; are hermetic, semi-hermetic, or open; are usually water cooled (via cooling tower, process source, well, or heating system); and range from 100 to thousands of tons. They have higher initial costs than reciprocating chillers and rarely provide direct expansion refrigeration but are relatively quiet, last a long time, are easily maintained, and can have low energy requirements per ton capacity. They are driven by electric drives (the majority), gas engines (nominal-cost standby, higher maintenance costs), or turbine drives (potentially quite economical if waste steam is used or the turbine supplies or retrofits low- pressure absorption-type chillers). (5) Absorption chillers use gas, steam, or hot water energy sources; require water for condensing; and are relatively quiet. Single- effect (low-pressure) chillers have high operating costs that can be reduced (e.g., cogeneration, waste heat use), offer a wide range of capacities, and have sensitive operation conditions. Double-effect (high-pressure) chillers improve operating efficiency and reduce energy use (by 50 percent compared to single-effect chillers), are fired directly or by high-pressure steam or high- temperature hot water, are cooled by water (less often, air in small units), range from 5 to 1,500 tons, and can be competitive with electric drive chillers under some rate schedules (see Figure 2.22).
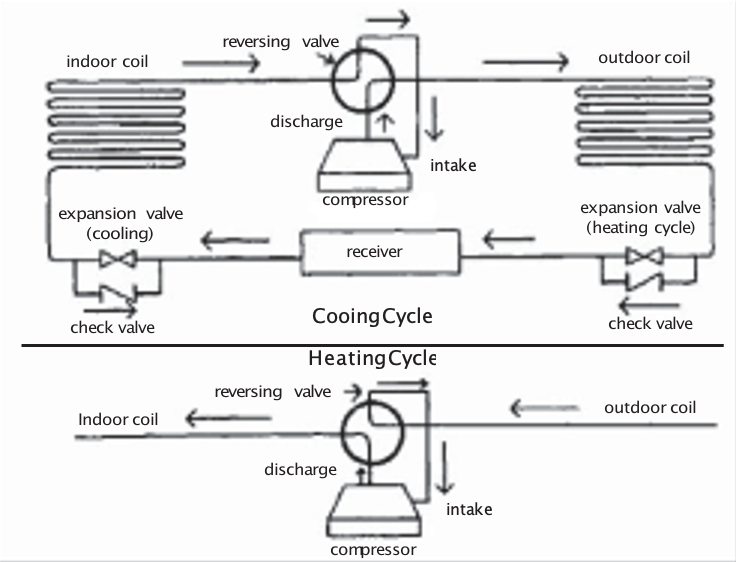
Figure 2.22. Typical Direct Expansion Refrigeration Cycle
Evaporative Coolers
In dry climates, water evaporation cools many (often single-zone) operations and raises relative humidity. Evaporative coolers are combined with mechanical refrigeration in more sophisticated systems. They are significantly cheaper as sole cooling sources and reduce energy needs and capital investment in combined systems. They provide some air cleaning but pose major maintenance and health problems because of mineral deposits and mildew. (1) Well-water cooling has a long U.S. history and covers most yearly cooling hours in many areas. It does not adversely affect water quality and availability, but tubes must be inspected and cleaned. Energy needs are one-third to one-fifth of other electric installations. Wells can replace cooling towers (e.g., often cheaper, year-round, no chemical use) and require very little space and maintenance. Well water has other uses (e.g., air precooling, irrigation, makeup water, fire protection, air conditioning in some states). (2) A heat rejection system (usually in a condenser transferring refrigeration cycle heat to the heat sink) is needed for all mechanical refrigeration systems. Condensing is provided by air-cooled refrigerant condensers, evaporative condensers, cooling towers, well (or other) water, or atmospheric cooling (each explained, including cost, advantages, disadvantages, maintenance). (3) A central chiller plant can serve all buildings, but the plant-building interface is key; each building usually needs its own pump; and temperature differentials must be managed in designs and operations.
Mechanical Distribution Systems
Piping System Components. Piping system design for building heating and cooling has evolved into five or six major systems, a few minor and little-used systems, and combinations (depending on building type and HVAC systems). Pipe placement is more restricted by steam systems than water systems. Selecting from the wide variety of piping depends on function (heating, cooling, both) and construction budget, avoiding elaborate piping that is more likely to fail (e.g., when heating and cooling systems interconnect). (See Figure 2.23.)
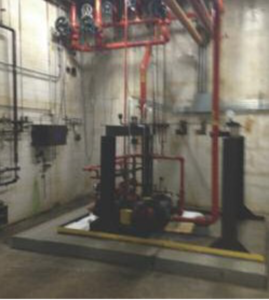
Figure 2.23. Example of a piping system for building heating and cooling.
Hot and Chilled Water Piping. The choice of type of piping system and valves greatly affects energy required for pumping and volumes of water to be pumped. One- pipe systems are not recommended for cooling.
Two-pipe systems are most common for heating and cooling, falling into direct return, often used because of installation economics, where water flow balance is key and the preferred reverse return, which tends to be self- balancing; combinations of reverse and direct return is not unusual. Three-pipe systems should not be used because of inaccurate water temperature control and wasted energy. Four-pipe systems use two sets of two- pipe systems (one for heating, one for cooling) based on need for simultaneous availability and are more costly; they should be investigated carefully (e.g., valve seals); many buildings can compromise with combined four- pipe and two-pipe systems.
Primary/Secondary Systems. Piping systems are operated with a single pumping source (one or more pumps operating in parallel), called the primary pumping systems. In some cases, primary/secondary pumping systems provide better control over water flow and required pressures. The primary system is a reservoir of cold or hot water circulating through a loop connected to all secondary systems, while the secondary pumping system serves a single air-handling unit, group of air- handling units, or entire building. Primary and secondary pumping systems are used to great advantage in a central chilled water plant, but problems can arise because of the imbalance caused by individual pump pressure added to the secondary system.
Steam Piping Systems. Steam systems are rarely used to heat modern buildings because water systems can handle both chilled and hot water and are easier to install. Steam systems are divided into similarly operating high-pressure systems and low pressure systems such as a one-pipe gravity return system (in some older homes acquired by universities), two-pipe gravity return system (more flexible, less water hammer noise), two-piped pumped return system (most common type), and vacuum return system (rare).
Piping Materials. The most widely used piping materials are copper and steel; the choice is usually based on initial costs. Not unusually, copper is used for pipe up to 2 inches in diameter and then steel; proper isolation connections are needed in such cases. Plastic piping is widely used in renovations because of ease of handling and fabrication and low fabrication costs; it must meet relevant standards and be supported per manufacturer recommendations for the operating temperature to avoid problems.
Pumps. Pumps move liquid through piping systems. The two types of pumps are positive displacement (normally reciprocating, sometimes rotary; limited only by plumbing system integrity) and non-positive displacement (usually centrifugal, normally driven by constant-speed electric , must be properly sized for proper pressure; most common pump in HVAC applications; simple design, low initial cost, easy to maintain, fairly quiet and vibration free). In all pumps, net positive suction head must be considered.
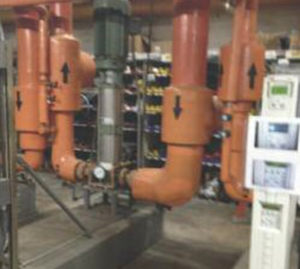
Figure 2.24. Examples of Valves
Valves. Valves placed at every piece of equipment isolate a system for maintenance or emergencies (e.g., gate, globe, and butterfly valves). Ball and plug valves are used more for balancing flow (required for all hydronic systems); balancing valves typically should not be used as shutoff valves. Opening and closing characteristics of a valve (in terms of flow) and pressure drop must be matched to the device controlled (see Figure 2.24).
Duct System Components
Duct systems have a big impact on initial and operating costs, but high quality is a good investment. SMACNA and ASHRAE set ductwork construction quality standards (on structural integrity, potential leakage), with classifications based on system air pressure. The lower the air velocity and pressure, the more economical the air distribution system. (1) A low-velocity/low-pressure system needs more space for installation and might have a higher initial cost, but lower operating costs make it most economical based on life-cycle costs; it uses rectangular (increasingly round) ductwork, has fewer structural demands, requires specifications for leakage (ranging from 25 percent to 1 percent), and is usually less noisy. (2) The traditional high-velocity/high-pressure system is generally unacceptable by energy conservation standards; it has 300 percent higher horsepower requirements and requires relatively high- quality duct construction but can reduce required duct cross-sectional area by as much as 60 percent.
Duct Material. Ductwork usually is galvanized sheet metal; ASHRAE and SMACNA have created well- established sheet metal gauges and construction methods. Systems can use fiberglass ductwork (moderate initial cost, low fan horsepower, quiet; subject to impact damage, air pressure consideration in design), flexible ductwork (low initial cost, good for tight spaces; potential to increase fan horsepower, limited in length to 4 feet, used in straight routes) and flexible connectors (NFPA standard compliance, code-limited length), lined ductwork (cheaper; modest fan horsepower penalty, not used if liner fibers can be entrained in delivery air), and special ductwork to deal with moisture, corrosive fumes, and greasy, dirty, or dusty air (e.g., fume hoods, food service exhaust hoods). Ductwork also requires (1) return air plenums (can greatly reduce costs, but must be constructed properly to avoid increasing energy costs, including meeting ductwork standards); (2) fans (move air through ductwork, same as compressors but lower pressures, Class 1 through III maximum total pressure standards), divided into two types, centrifugal and axial flow (e.g., propeller, tube axial, and vane axial fans); (3) dampers, which are to ductwork what valves are to piping systems, such as parallel blade (best for shutoffs), opposed blade (where modulating control is needed), and fire rated, smoke rated, or combined dampers (where ductwork penetrates walls and floors; sometimes connected to a fire alarm system); and (4) other components to enhance operating characteristics (e.g., turning vanes, sound attenuators, transition sections, bell mouth entrances, transition takeoffs).
HVAC Systems
The building mechanical system can include several of the basic air conditioning system types, creating infinite combinations, often dictated by differences in temperature and humidity control requirements.
All-Air Systems. These systems have heating and cooling equipment (e.g., coils, fans, filters) at a central site (e.g., mechanical room) and distribute conditioned air through ductwork, with many advantages (e.g., centralized equipment, option to cool with outside air, wide choice of zones, easy humidity control, return air or exhaust fans to improve control of air circulation and building pressurization).
Single-Zone Systems. This is the most fundamental type, with a fan drawing air through coils (draw-through system), and succeeds only if all zone spaces have similar external weather exposure and similar occupancies and operations. A building can use multiple single-zone systems; if one fails, other zones are unaffected. These systems are simple and easy to maintain but limited to relatively small areas; too many single-zone systems in a large building increase cost, maintenance, and space requirements.
Multi-zone Systems. These air-handling systems (usually low-velocity low-pressure, with moderate fan horsepower) use the same components as single-zone systems but mix warm and cold air to simultaneous temperatures for different zones, deliver it in separate ducts, and offer individual space temperature control. They have low initial costs, but fixed zone ducts must be changed for remodeling or load increases, and inefficiencies arise in heating season when certain areas require year-round cooling.
Reheat Systems. A variation of an all-air system, reheat systems are installed in zone ducts (with a steam, hot water, recovered heat, or electric heating coil). They control both space temperature and humidity; sophisticated humidity control reheat systems are often one-zone systems (e.g., computer rooms). Reheat systems are generally undesirable unless using recovered heat. They have high energy costs during the summer; generally require careful maintenance, control calibration, and monitoring; can pose problems in tight spaces; are limited by energy codes; and are relatively inflexible.
Dual-Duct Systems
Dual-duct constant-volume systems easily achieve balanced airflow and maintain individual zone temperatures. Recent systems are medium or low pressure, reducing horsepower needs. They resemble multi-zone systems in arrangement and in-duct temperature control; except for modified units, they have the same inherent winter inefficiency in the mixed air cycle. They are relatively high in initial cost and require an extra duct and extra depth (minimized by careful planning) but offer greater operation economies and can be modified for variable volume air flow.
Variable Air Volume Systems
Space temperature can be controlled in two ways: deliver a constant volume of air and vary supply air temperature or deliver air at a constant temperature and vary quantity of air (i.e., VAV systems). These systems are more popular as single-duct, cooling-only, draw- through zone-level technology has improved. Power requirements to move air vary by the cube law, with fan power savings for heating and cooling systems with low load requirements, but at low loads, air quantities are often greatly reduced, causing poor air circulation; solutions include fan-powered terminals, supply air temperature control, and air duct zoning. Placing heating coils at terminals forms a reheat system (like a multi-zone system). VAV systems can have noise problems. They are flexible and cost the same or less than dual-duct systems.
Specialty Air Systems
Heat Recovery. Used for years in power and industrial plants and subarctic homes, heat recovery levels are as high as 80 percent and can be the only way to reduce older building energy costs, especially if 100 percent ventilated air is needed (e.g., medical facilities). (1) Air- to-air heat recovery systems have as high as 65 percent efficiency. At recovery point, exhaust and supply air streams must be adjacent, so use is limited if air streams are contaminated (unless seals and pre-filtering purge units are used). These systems are easy to clean but require effectively designed and maintained filtration systems. Heat pipe/coil equipment, a type of air-to-air recovery based on refrigeration cycle, is easily maintained and has efficiencies as high as 80 percent. (2) Runaround systems are used for non-adjacent air streams (and retrofits), energy transfer within buildings, and heat recovery from activities such as laundries that use high quantities of hot water; efficiency is as high as 45 percent. Added in cold climates, antifreeze reduces efficiency and increases pumping costs. (3) Plate-type heat exchangers are used when heat must be transferred from one water or air system to the other while keeping streams separate. They are efficient, easily installed, and easily maintained, with efficiencies as high as 70 percent, but large sizes are required to avoid high-pressure drops.
Laboratory Fume Hoods
Fume hoods are a specialized part of the total ventilation system to exhaust toxic gases, contaminants, and noxious odors outside, protecting laboratory users, nearby people, and the environment. Main users are chemical and biological laboratories. AHSRAE handbooks provide information on fume hood design.
This section describes important factors such as (1) fume hood location because the hood affects HVAC systems, and location affects stable airflow into the fume hood face; (2) face velocity because air velocity is a key factor in safe performance; fume hoods are tested per SAMA Standard LF 10-1980, with velocity readings once a year and after blower or duct changes, repairs and HVAC modifications and with new installations and remodels tested before use; (3) fume hood construction because materials and construction method must match use; many standard, common, and special optional features are available, as are several fume hood sash designs; and (4) exhaust system because a single exhaust blower for each hood can be utilized (a good option if budget allows) or multiple hoods on one exhaust system (which lowers cost, reduces needed ductwork, and improves aesthetics, although pressure and backflow issues must be addressed for proper operation); materials depend on use; stacks must be designed properly for safety and dispersal; and makeup air volumes must vary.
Maintenance. Maintenance and laboratory personnel must be trained in university procedures for routine maintenance (e.g., no repairs or filter changes without exhaust system shutdown; protective clothing and respirators for hood and exhaust work; shutdown of fume hood activity and capping or removal of chemicals) and emergency (system failure) repairs (e.g., shutdown of fume hood activity and capping or removal of chemicals, all parts tested for contamination before repair and decontaminated by qualified technicians if needed). All users should receive advance notice of maintenance shutdowns. Preventive maintenance enhances reliable performance and reduces potential safety liability issues.
Chemical Fume Hoods. Probably the most common type, chemical fume hoods are used for low and moderate hazard processes, are most often used where materials and procedures are known, and have an indicating manometer for functionality.
Canopy Hoods. These hoods vent heat and smoke; they are not chemical and research fume hoods.
Biological Safety Cabinets. These cabinets (also safety cabinets or ventilated safety cabinets) come in two sizes (4 foot and 6 foot) and four classes: Class I, a partial containment cabinet (10 percent exhaust system) protects people and is for flammables, animal autopsies, and low biological agents; Class II-A has a fixed opening, recirculates 70 percent of air, protects people and research materials, and is not for flammable, toxic, or radioactive materials; Class II-B maintains inward airflow, recirculates 30 percent of air and exhausts 70 percent through the work area, and is for low-level volatiles and carcinogen trace levels in tissue cultures; and Class III is a specially designed gas-tight negative-pressure containment system (100 percent exhaust from building) for high-risk biological, chemical, and radioactive materials.
Other Design Issues. (1) Laminar flow hood designs are for product (not worker) protection and are not recommended for biological, chemical, or radioisotope worker protection. (2) Effects on HVAC systems have produced more sophisticated HVAC systems for airflow balancing, including fume hood exhaust air. (3) Energy conservation (e.g., fume hoods equipped with auxiliary air supplies) is useful in retrofits.
Hydronic Systems
Air-Water Systems. In these systems, both air and water are distributed throughout building spaces for heating or cooling. (1) Fan coil systems, one of the earliest air-water systems, are quiet, easy to maintain, and simple to operate; offer individual space temperature control; and are used on building perimeters. They use two-pipe or four-pipe systems and are relatively energy efficient (usually a three-speed motor). They are breeding grounds for bacteria and are not used if clean air is important. (2) Fin tube heating and cooling is perhaps the most common type (e.g., radiator-type units), with single or stacked fins and a variety of metal covers. Fin tubes use steam or hot water as a source; achieve control via a manual valve, automatic valve, or water temperature control; and provide a blanket of air at the building perimeter. Fin tube radiation is often used with cooling-only VAV systems. (3) Convectors are similar to fin tubes, but can use a small coil heating element (similar to fan coil) and fit in smaller spaces. (4) Unit ventilators are a variation of the fan coil system but generally larger and can heat and cool larger spaces. They are often installed with fin tube radiation or auxiliary air ducts. They use quiet fans and low fan horsepower (less than all-air systems) and are relatively simple to maintain.
Induction Systems
This section describes induction systems, traditionally high-velocity systems using small round ducts and a coil that can be used for heating and cooling. New low- pressure designs save energy. They can circulate total required air space without an in-unit fan, relying on the main fan system, but have high fan horsepower requirements. Induction systems provide individual space control (little or no contamination across rooms), quiet operation, and minimum maintenance. They are not highly flexible, but multiple units usually cover most needs. They are widely used in offices and dorms.
Hot Water Heating
Hot water heating system advantages include small pipe sizes, routing flexibility, ease of zoning, varying water temperature, quiet operation, and low pumping costs.
Such systems can combine with chilled water systems to provide heating and air conditioning in the same piping system, often via the same device (e.g., fan coil or air-handling unit). They should be balanced at start-up. There is little or no corrosion if properly operated and maintained. They can be zoned like a steam system; temperature reset produces lower heat losses and greater energy economies. They are often used with all- air and VAV systems.
Steam Heating
Steam heating pressures rarely exceed 125 pounds. Low-pressure systems use moderate steam temperatures compared to higher pressure steam and low-pressure boilers; require less stringent monitoring under most codes; and can be distributed without pumps (unlike hot water heating systems). Steam heating systems using radiators directly within the space are rare now but still common in older buildings. Disadvantages include excessively hot temperatures most of the time (e.g., radiation, piping, system), difficult piping installation, large supply pipe sizes, tendency of return line to corrode, space required by horizontal runs, and need for careful steam trap maintenance to avoid leaks and high fuel use (20 to 25 percent of building energy use). Some systems operate under sub- atmospheric and vacuum conditions and produce steam at lower temperatures but require good maintenance; low-pressure steam can supply needed heat for coils in air-handling units (but tends to freeze rapidly when heating fresh air). Steam can be zoned in much the same manner as air systems. Steam systems with perimeter radiation can support installation of VAV or air conditioning in a remodeled building.
Leave a Reply
You must be logged in to post a comment.